How to Improve Steel Wire Rewinding Machine Efficiency in Multi-Product Distribution Centers?
In multi-product distribution centers, optimizing steel wire rewinding machine productivity improvements is critical. Streamlining this process reduces bottlenecks, minimizes downtime, and ultimately enhances overall operational efficiency, leading to significant cost savings and improved customer satisfaction.

Improving steel wire rewinding machine efficiency involves several key strategies. These include regular maintenance, operator training, automation upgrades, optimized material handling, and implementing real-time monitoring systems to detect and address inefficiencies promptly. By focusing on these areas, distribution centers can significantly boost their rewinding operations.
The need for efficiency is constant, and optimizing your wire rewinding process is an ongoing journey. Let’s dive into some actionable methods you can employ to maximize output and minimize waste.
1. Implementing a Robust Maintenance Program
A proactive maintenance program is the cornerstone of any efficient steel wire rewinding operation. Neglecting maintenance leads to breakdowns, reduced machine lifespan, and decreased Collection.
Regular maintenance is crucial for maintaining the efficiency of steel wire rewinding machines. This includes scheduled inspections, lubrication, cleaning, and timely replacement of worn parts. A well-maintained machine operates smoothly, reduces downtime, and ensures consistent performance, ultimately boosting productivity. This isn’t just about fixing things when they break; it’s about preventing them from breaking in the first place.
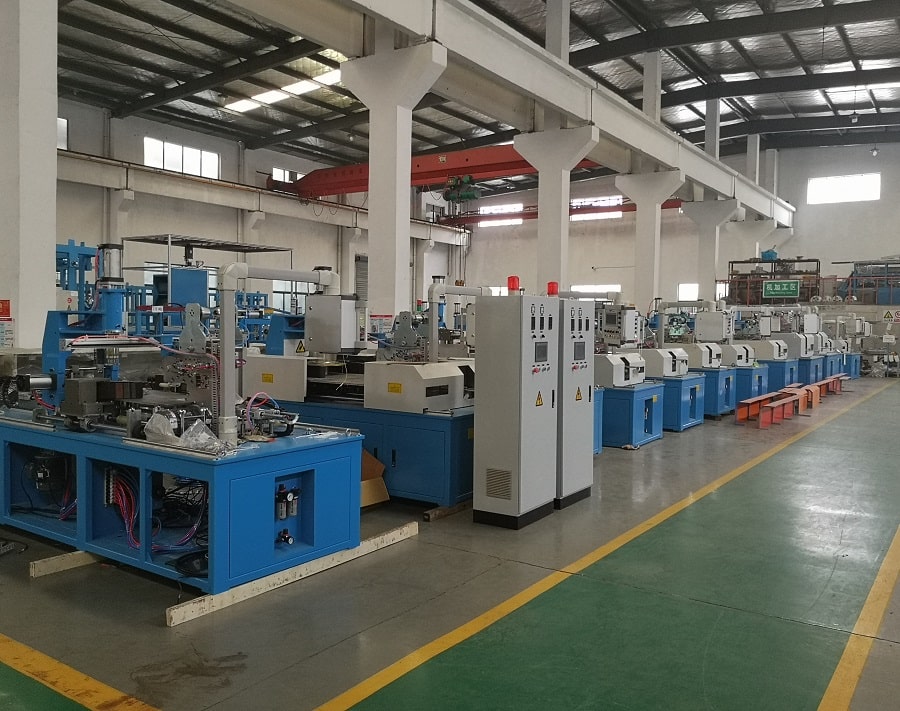
Understanding Predictive vs. Reactive Maintenance:
The key to a successful maintenance program is understanding the difference between reactive and predictive maintenance. Reactive maintenance is simply fixing a problem after it occurs, while predictive maintenance uses data and monitoring to anticipate potential issues. Predictive maintenance can save significant time and resources.
Benefits of Predictive Maintenance
Switching to a predictive maintenance model brings various advantages:
- Reduced Downtime: By identifying potential problems before they lead to breakdowns, predictive maintenance minimizes unexpected downtime and keeps the productivity improvements rolling.
- Extended Machine Lifespan: Regular maintenance and timely repairs extend the lifespan of the rewinding machine, providing a higher return on investment.
- Improved Operational Efficiency: A well-maintained machine operates at peak performance, ensuring consistent quality and maximum output.
- Cost Savings: Preventative measures are often less expensive than emergency repairs, leading to substantial cost savings in the long run.
Components of a Maintenance Plan
Creating a maintenance plan requires careful consideration and understanding of the rewinding machine’s specific needs. Here’s a breakdown of the key components:
- Scheduled Inspections: Regular inspections should be conducted to identify wear and tear, loose connections, and any other potential issues.
- Lubrication: Proper lubrication of moving parts is essential for smooth operation and reduces friction, extending the lifespan of components.
- Cleaning: Regular cleaning removes debris and contaminants that can affect performance and cause damage.
- Parts Replacement: Worn or damaged parts should be replaced promptly to prevent further damage and maintain optimal performance.
- Monitoring Systems: Implementing real-time monitoring systems can help detect unusual vibrations, temperature fluctuations, or other anomalies that may indicate a problem.
- Data Analysis: Analyzing data collected from inspections and monitoring systems can help identify trends and predict potential issues, enabling proactive maintenance.
A detailed maintenance log should be kept, documenting all inspections, repairs, and parts replacements. This information can be used to track machine performance, identify recurring problems, and optimize the maintenance schedule.
Implementing a Maintenance Schedule
Task | Frequency | Description |
---|---|---|
Visual Inspection | Daily | Check for loose connections, leaks, or unusual wear. |
Lubrication | Weekly | Lubricate all moving parts according to manufacturer’s recommendations. |
Cleaning | Monthly | Remove debris and contaminants from the machine. |
Parts Replacement | Quarterly | Replace worn or damaged parts. |
System Calibration | Annually | Calibrate the machine to ensure accurate and consistent performance. |
Data Analysis | Bi-Annually | Analyze maintenance logs and monitoring data to identify trends. |
By implementing a comprehensive maintenance program that includes regular inspections, lubrication, cleaning, parts replacement, monitoring systems, and data analysis, distribution centers can significantly improve steel wire rewinding machine efficiency and reduce operational costs.
2. Prioritizing Operator Training and Skill Development
Even the most advanced rewinding machine is only as good as the operator who runs it. Proper training and skill development are essential for maximizing Steel wire rewinding machine efficiency and minimizing errors.
Well-trained operators are crucial for maximizing rewinding machine efficiency. They can operate the machine safely and effectively, troubleshoot minor issues, and identify potential problems before they escalate. Training should cover machine operation, maintenance procedures, and safety protocols to ensure optimal performance.

The Impact of Skilled Operators
Skilled operators bring several advantages:
- Increased Productivity: Trained operators can operate the machine at its optimal speed and efficiency, maximizing output.
- Reduced Errors: Proper training minimizes errors and reduces the risk of damaging the wire or the machine.
- Improved Safety: Trained operators are aware of safety protocols and can operate the machine safely, preventing accidents and injuries.
- Faster Troubleshooting: Skilled operators can quickly identify and troubleshoot minor issues, reducing downtime.
- Better Maintenance: Trained operators can perform basic maintenance tasks, helping to keep the machine in good working order.
Developing a Comprehensive Training Program
A comprehensive training program should include both theoretical and practical components. Here are some key elements to consider:
- Machine Operation: Operators should receive thorough training on all aspects of machine operation, including startup, shutdown, speed control, and tension adjustment.
- Maintenance Procedures: Operators should be trained on basic maintenance tasks, such as lubrication, cleaning, and parts replacement.
- Safety Protocols: Operators should be fully aware of all safety protocols and procedures, including emergency shutdown procedures and personal protective equipment requirements.
- Troubleshooting: Operators should be trained to identify and troubleshoot common problems, such as wire breaks, tension fluctuations, and alignment issues.
- Continuous Learning: Operators should receive ongoing training and skill development to stay up-to-date with new technologies and best practices.
This can involve external courses, on-site workshops, or even mentorship programs pairing experienced operators with newer team members.
The best training programs also incorporate hands-on experience. Operators should be given ample opportunity to practice operating the machine under the supervision of experienced trainers. This allows them to develop the skills and confidence they need to perform their jobs effectively.
Benefits of Investing in Operator Training
Investing in operator training offers numerous benefits, including:
- Reduced downtime: Skilled operators can quickly troubleshoot and resolve minor issues, minimizing downtime.
- Improved product quality: Trained operators can ensure that the wire is rewound to the correct specifications, resulting in higher quality products.
- Increased efficiency: Skilled operators can operate the machine at its optimal speed and efficiency, maximizing output.
3. Automating for Enhanced Efficiency
Introducing automation into your steel wire rewinding process can significantly enhance efficiency and reduce manual labor, even with multi-product distribution.
Automation is a key strategy for boosting efficiency in steel wire rewinding operations. By automating tasks such as wire feeding, tension control, and spool changes, distribution centers can reduce manual labor, increase throughput, and improve product quality.
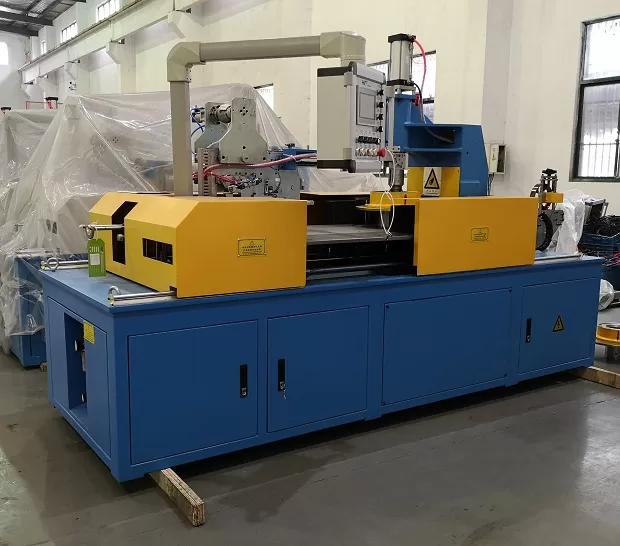
Key Automation Opportunities in Rewinding
- Automated Spool Changing: Automating the process of changing spools reduces downtime and increases throughput, especially when dealing with varied wire gauges and spool sizes in a multi-product environment.
- Automated Tension Control: Automated tension control systems ensure consistent wire tension throughout the rewinding process, resulting in higher quality products and reduced wire breaks.
- Robotic Wire Handling: Robots can be used to handle wire spools, load and unload machines, and perform other repetitive tasks, reducing manual labor and improving safety.
- Real-Time Monitoring: Integrate sensors and software to monitor tension, speed, and other critical parameters in real-time. This data helps identify potential issues and optimize performance.
Selecting the Right Automation Solutions
Choosing the appropriate automation solutions requires careful consideration of your specific needs and budget. Here are some factors to consider:
- Scalability: Choose automation solutions that can be scaled up or down to meet changing production demands.
- Integration: Ensure that the automation systems can be easily integrated with existing equipment and systems.
- Flexibility: Opt for automation solutions that can handle a variety of wire types, spool sizes, and rewinding parameters.
- Cost-Effectiveness: Evaluate the cost of the automation solutions against the potential benefits, such as reduced labor costs, increased throughput, and improved product quality.
Automating certain processes delivers a transformative effect.
Levels of Automation
Automation Level | Description | Benefits |
---|---|---|
Basic | Semi-automated systems with manual loading and unloading. | Reduced labor, increased throughput, improved product quality. |
Intermediate | Systems with automated spool changing and tension control. | Further reduced labor, increased throughput, improved consistency, reduced waste. |
Advanced | Fully automated systems with robotic wire handling and real-time monitoring. | Maximum throughput, minimal labor, optimized performance, predictive maintenance, enhanced safety, improved traceability. |
By carefully evaluating your needs and selecting the right automation solutions, you can significantly improve steel wire rewinding machine efficiency and reduce operational costs in your multi-product distribution center.
4. Optimizing Material Handling and Logistics
Streamlining material handling and logistics is critical for minimizing downtime and ensuring a smooth flow of materials in and out of the rewinding area.

Effective material handling is vital in distribution centers. Efficient storage, transportation, and accessibility of materials minimizes delays and supports continuous rewinding operations. Proper organization reduces downtime and improves overall productivity.
Material Handling Strategies
Properly Arranging your Material Storage
Proper Storage can minimize delays and keep operations running smoothly
- Raw Material: Having a storage area will increase workflow.
- Having proper tools: tools and proper tools will assist in movement
Enhance Layout for Material transportation
- Transportation: Streamline by using conveyor belts
- Minimizing walking distance: Minimize distance by proper set up
Applying proper Inventory Management
Proper Inventory Management will decrease storage space.
- Use Lean manufacturing to minimize work
- Having the right tools will help improve this process
Conclusion:
Improving steel wire rewinding machine efficiency in multi-product distribution centers requires a holistic approach. By focusing on maintenance, training, automation, and material handling, distribution centers can unlock significant Steel wire rewinding machine efficiency, reduce operational costs, and deliver higher-quality products to their customers.