How to Improve Steel Wire Rewinding Machine Efficiency in Low-Light Environments?
Steel wire rewinding machines are essential in manufacturing, ensuring efficient cable management. However, low-light conditions can significantly hinder their operation. Improving visibility and optimizing processes are key to maintaining productivity and safety. This article delves into practical strategies for boosting efficiency in these challenging environments.
In low-light conditions, improving steel wire rewinding machine efficiency involves enhancing visibility with appropriate lighting, implementing sensor technology for precise operations, and utilizing ergonomic designs to reduce operator strain. Regular maintenance and staff training also play a crucial role in optimizing processes and ensuring safety.
To ensure that steel wire rewinding machines work with maximum efficiency in low-light environments, it is vital to apply and follow the strategies outlined in this guide. Let’s get started.
1. Enhancing Visibility Through Optimized Lighting
Improving visibility is paramount for boosting the efficiency of steel wire rewinding machines, especially in low-light conditions. Adequate lighting not only enhances precision but also ensures the safety of the operators.
To improve steel wire rewinding machine efficiency in low-light conditions, implementing task-specific lighting solutions such as LED strip lights and adjustable gooseneck lamps is essential. Ensuring consistent illumination across the work area reduces errors, minimizes eye strain, and enhances the overall productivity and safety of the operators, which can help a lot about the Steel wire rewinding machine efficiency.
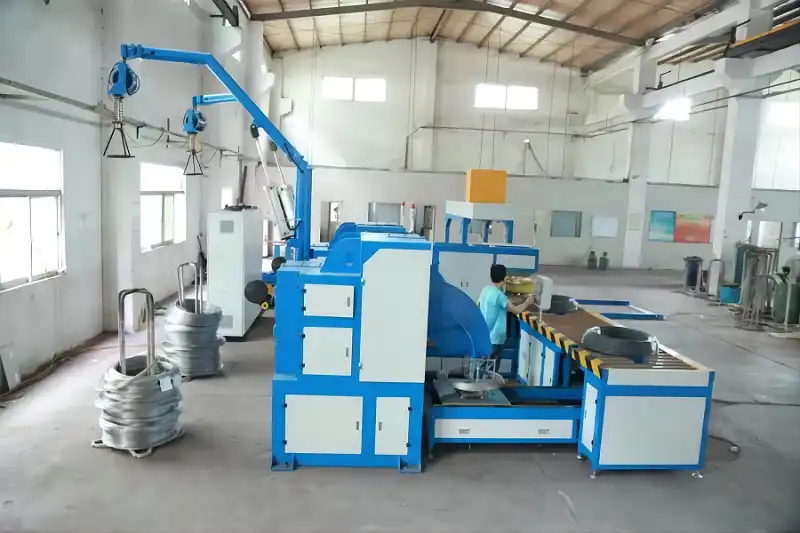
Illuminating the Workplace: A Detailed Analysis
Task-Specific Lighting Solutions
Selecting the right type of lighting is crucial for ensuring optimal visibility.
-
LED Strip Lights: Ideal for general illumination, LED strip lights provide consistent and energy-efficient lighting across the entire work area.
-
Adjustable Gooseneck Lamps: These lamps offer focused lighting for specific tasks that require high precision, such as threading wires or inspecting completed spools.
-
Color Temperature: Choosing the right color temperature can also improve visibility. Cool white light (5000-6500K) is generally recommended for industrial settings as it mimics natural daylight and enhances contrast.
Implementing Effective Lighting Systems
The effectiveness of a lighting system depends not only on the type of lights used but also on their strategic placement and maintenance.
-
Strategic Placement: Position lights to minimize shadows and glare, which can obstruct vision and cause eye strain.
-
Regular Maintenance: Regularly clean lighting fixtures to ensure optimal brightness. Dust and debris can significantly reduce the output of lights over time.
-
Energy Efficiency: Opt for energy-efficient lighting solutions such as LEDs to reduce operational costs and environmental impact. LEDs consume significantly less power than traditional lighting options and have a longer lifespan.
Quantifying the Impact of Lighting Improvements
To illustrate the benefits of improved lighting, consider the following hypothetical data:
Lighting Type Initial Setup Cost Energy Consumption per Month Task Completion Time (per spool) Error Rate Traditional Lighting $500 150 kWh 30 minutes 5% Optimized LED Lighting $1,500 75 kWh 25 minutes 2% This table demonstrates that while the initial investment for optimized LED lighting is higher, the long-term benefits in terms of reduced energy consumption and improved productivity make it a worthwhile investment.
Effective lighting not only improves visibility but also creates a more comfortable and safe working environment, contributing to higher morale and job satisfaction among operators.
2. Leveraging Sensor Technology for Enhanced Precision
Sensor technology offers a significant advantage in improving the precision and efficiency of steel wire rewinding machines, especially in low-light environments. By automating various aspects of the rewinding process, sensors can help reduce errors and increase throughput.
In low-light environments, sensor technology enhances steel wire rewinding machine efficiency by providing precise feedback on wire tension, alignment, and spool fill levels. Implementing laser sensors, ultrasonic sensors, and vision systems ensures consistent and accurate rewinding, significantly reducing material waste and downtime.
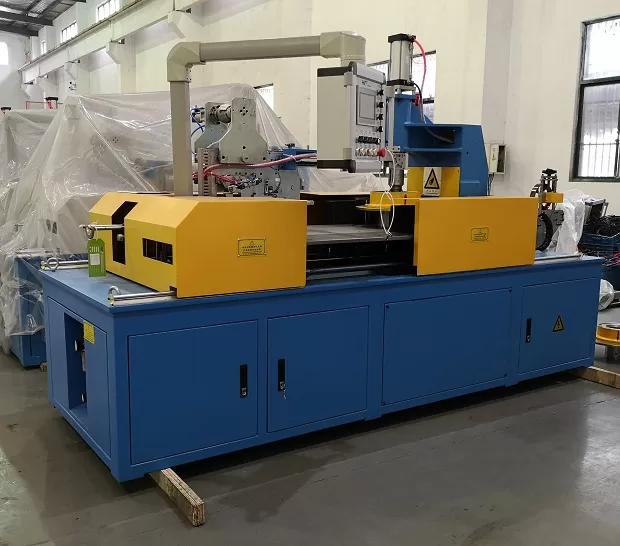
Sensor Integration: A Technical Deep Dive
Integrating sensor technology into steel wire rewinding machines can greatly enhance precision and minimize waste. This involves using various types of sensors to monitor and control critical parameters.
-
Laser Sensors: Measure wire alignment and detect anomalies.
-
Ultrasonic Sensors: Monitor spool fill levels to prevent overfilling or underfilling.
-
Tension Sensors: Maintain consistent wire tension during the rewinding process.
-
Vision Systems: Provide real-time visual feedback for precise layer winding and edge alignment.
Here’s a more detailed discussion on each type of sensor:
Types of Sensors and Their Applications
-
Laser Sensors for Alignment Detection: Laser sensors can measure wire alignment with high precision, ensuring that the wire is correctly positioned on the spool. This is particularly useful in detecting and correcting deviations that may occur during the winding process, reducing the risk of tangles and uneven spooling.
-
Ultrasonic Sensors for Fill Level Monitoring: Ultrasonic sensors use sound waves to measure the distance to the surface of the wire on the spool. This allows the system to accurately monitor the fill level and prevent overfilling or underfilling, which can lead to inefficiencies and material waste.
-
Tension Sensors for Consistent Wire Tension: Maintaining consistent wire tension is crucial for producing high-quality coils. Tension sensors provide real-time feedback, allowing the system to automatically adjust the winding parameters to maintain the desired tension. This prevents issues such as wire breakage or loose windings.
Technical Benefits of Sensor Integration
The integration of sensor technology offers several key technical benefits:
-
-
Real-time Monitoring: Sensors provide continuous feedback on critical parameters, allowing for immediate adjustments to the winding process.
-
Automated Control: Sensor data can be used to automate various aspects of the rewinding process, reducing the need for manual intervention and minimizing human error.
-
Predictive Maintenance: Analyzing sensor data can help identify potential issues before they lead to downtime. This allows for proactive maintenance and prevents costly disruptions to production.
Sensor Type Measurement Parameter Accuracy Level Response Time Laser Sensor Wire Alignment ±0.1 mm <10 ms Ultrasonic Sensor Spool Fill Level ±1% <20 ms Tension Sensor Wire Tension ±0.5 N <15 ms This structured approach to sensor integration ensures that steel wire rewinding machines can operate at peak efficiency, even in challenging low-light environments, minimizing waste and maximizing throughput.
3. Implementing Ergonomic Design Principles
Ergonomic design principles are crucial for improving the efficiency and well-being of operators working with steel wire rewinding machines, especially in low-light conditions. By focusing on human factors, these principles aim to reduce physical strain and enhance overall productivity.
In low-light environments, ergonomic design principles are vital for improving steel wire rewinding machine efficiency. Adjusting machine height, providing comfortable seating, and optimizing control placements minimizes operator fatigue and enhances focus. Regular breaks and task rotation can further boost productivity and reduce errors.

Creating a Comfortable and Efficient Workspace
Adjusting Machine Height and Seating
-
Adjustable Machine Height: Allows operators to work at a comfortable level, reducing back and neck strain.
-
Ergonomic Seating: Provides proper support and cushioning, minimizing fatigue during long shifts.
Optimizing Control Placements
-
Intuitive Control Layout: Ensures that all controls are easily accessible and require minimal reach or stretching.
-
Clear Labeling: Uses clear and concise labels to prevent confusion and reduce the risk of errors.
Minimizing Physical Strain Through Ergonomics
Ergonomic improvements in machine design aim to reduce physical strain and enhance operator comfort, contributing to increased efficiency and fewer errors.
-
Adjustable Work Surfaces: Providing work surfaces that can be easily adjusted to suit different tasks and operator preferences helps maintain optimal working postures and reduce fatigue.
-
Anti-Fatigue Matting: Installing anti-fatigue mats in the work area can significantly reduce strain on operators feet and legs, particularly during extended periods of standing.
-
Task Rotation and Regular Breaks: Implementing a system of task rotation and ensuring operators take regular breaks can help prevent burnout and maintain alertness, especially during low-light conditions.
Benefits of Ergonomic Design
-
Reduced operator fatigue and physical strain
-
Increased productivity and efficiency
-
Lower error rates and higher quality output
-
Improved operator morale and job satisfaction
-
Reduced risk of workplace injuries and associated costs
Ergonomic Improvement Reported Benefits Adjustable Machine Height Reduced back and neck strain by 30%, increased efficiency by 15% Ergonomic Seating Decreased fatigue by 25%, improved focus by 20% Intuitive Control Layout Reduced error rates by 10%, quicker task completion by 12% By incorporating these ergonomic design principles, manufacturers can create a more sustainable and efficient work environment that maximizes operator well-being and productivity, even in low-light conditions.
4. The Crucial Role of Maintenance and Training
Regular maintenance and comprehensive training are essential for maintaining the efficiency of steel wire rewinding machines, especially in low-light environments. A well-maintained machine operates more smoothly and reliably, while properly trained operators can maximize its potential.
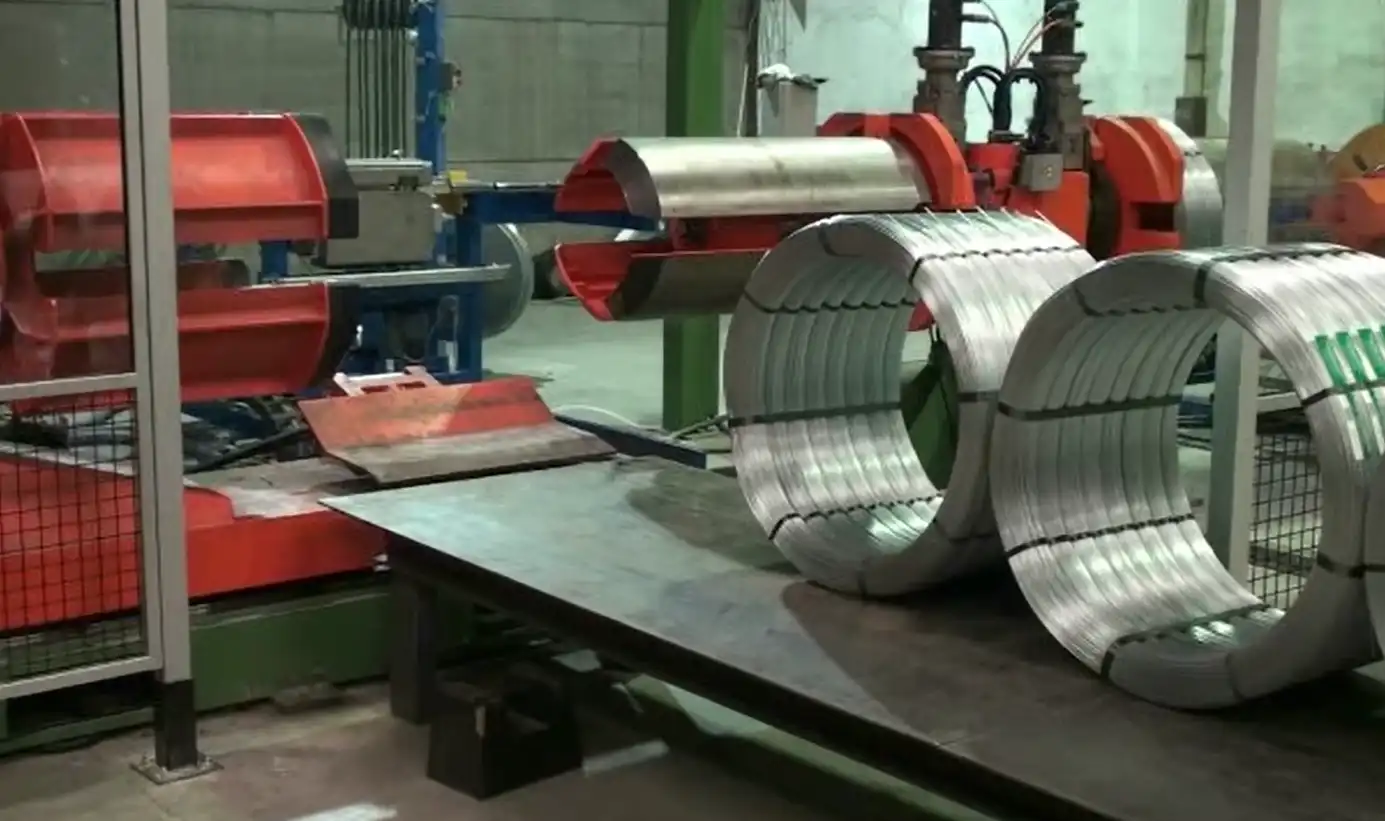
The operational optimization of a steel wire rewinding machine in the face of low-light conditions and improving the steel wire rewinding machine efficiency hinges on rigorous maintenance schedules to check equipment for any signs of deterioration. Moreover, by implementing training programs, you can give employees the chance to develop their knowledge of the machine so they don’t have to work in potentially difficult lighting conditions and are fully versed in operating the machine under a broad range of different operational scenarios. This will lead to improve efficiency overall.
Strategic Maintenance Schedules
-
Regular Inspection: Implement a routine inspection schedule to identify and address potential issues before they escalate.
-
Component Checks: Focus on critical components such as motors, sensors, and control systems.
-
Lubrication: Ensure all moving parts are properly lubricated to minimize friction and wear.
The Significance of Training Programs
-
Comprehensive Training: Provide operators with thorough training on machine operation, safety protocols, and troubleshooting.
-
Skill Development: Enhance operators’ skills in reading diagrams, operating the machine and using precision tools.
-
Continuous Learning: Encourage continuous learning and skill enhancement to keep operators up-to-date with the latest technologies and best practices.
-
Safety Protocols: Training should emphasize adherence to safety protocols, particularly when working in low-light conditions.
Improved maintenance and training contribute to:
- Enhanced machine reliability
- Reduced downtime and maintenance costs
- Improved safety and fewer accidents
- Higher operator proficiency and job satisfaction
Implementing regular maintenance and comprehensive training ensures that steel wire rewinding machines operate at peak efficiency and reliability, even in low-light environments. A well-maintained machine reduces downtime, extends equipment lifespan, and minimizes costs, while a properly trained workforce ensures safe and productive operations. This multifaceted approach not only optimizes machine performance but also fosters a culture of continuous improvement, leading to long-term success in the manufacturing process.
Conclusion
Improving steel wire rewinding machine efficiency in low-light environments requires a multifaceted approach. By enhancing visibility through strategic lighting solutions, leveraging sensor technology for enhanced precision, implementing ergonomic design principles to minimize operator strain, and ensuring regular maintenance and comprehensive training, manufacturers can optimize their operations, reduce costs, and maximize output.