How to Improve Pipe Bundling Machine Efficiency in Low-Cost Operations?
Improving pipe bundling machine efficiency in low-cost operations requires a strategic approach. This involves optimizing existing processes, investing in cost-effective upgrades, and implementing smart maintenance practices. The goal is to maximize output while minimizing expenses.
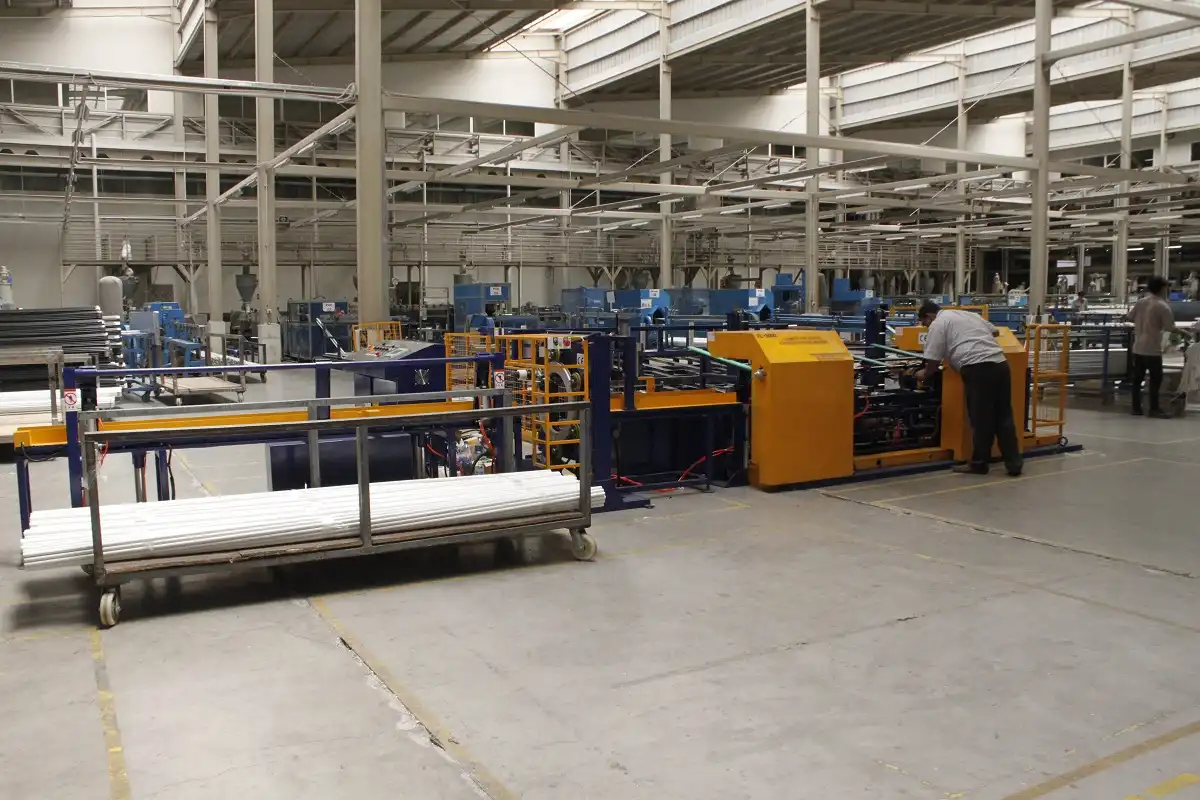
To enhance pipe bundling machine efficiency in low-cost setups, focus on streamlining workflows and reducing material waste. Regular maintenance, operator training, and selecting appropriate bundling materials are crucial. Consider modular upgrades to improve automation without significant capital expenditure.
Are you looking to maximize your pipe bundling operations’ output without breaking the bank? Read on to discover practical strategies for achieving optimal efficiency in a low-cost environment.
1. Optimizing Existing Pipe Bundling Machine Operations
Efficient operations start with a thorough understanding of your current processes. Let’s explore how to refine your existing workflows for better results.
To optimize existing pipe packaging machines operations, start with a detailed analysis of the current workflow. Identify bottlenecks, areas of material waste, and opportunities for process streamlining. Regular maintenance and operator training are also key to maximizing machine uptime and performance.
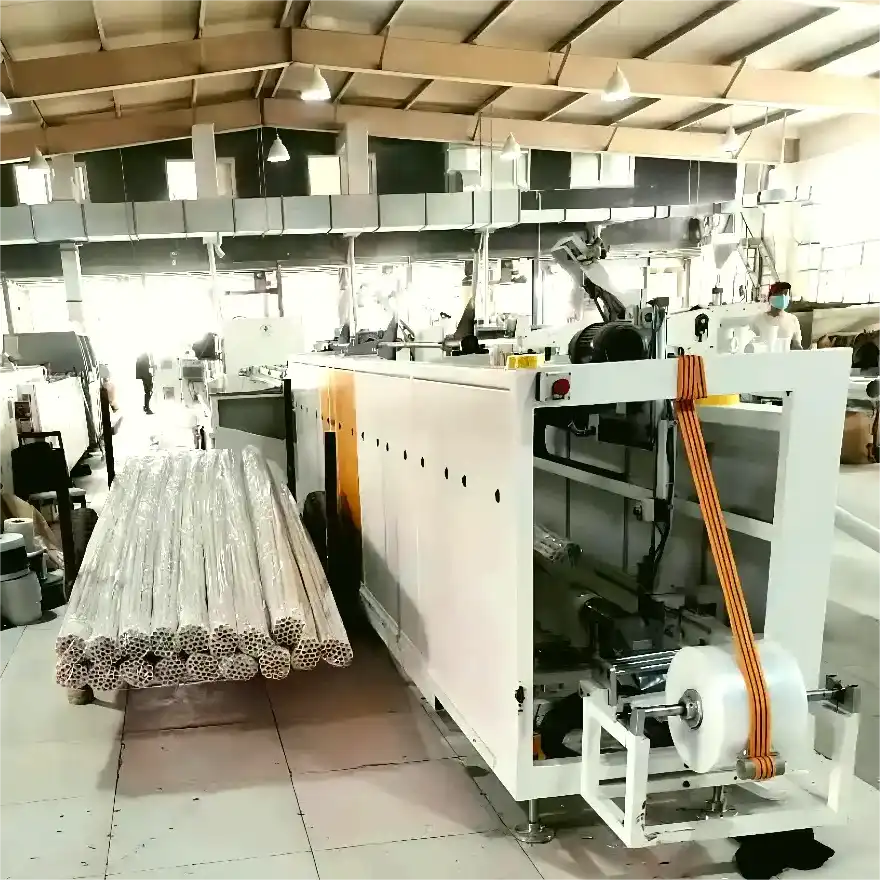
Streamlining for Success: A Deep Dive into Efficiency
To truly elevate your pipe bundling machine efficiency within a budget-conscious framework, it’s essential to dissect every aspect of your current workflow. This involves identifying inefficiencies and implementing targeted solutions.
1.1 Analyzing the Current Workflow
Begin by meticulously mapping out your current pipe bundling process. This includes everything from pipe feeding and alignment to bundling, strapping, and ejection. Look for areas where bottlenecks occur, where material waste is high, or where manual intervention slows things down.
1.2 Identifying Bottlenecks
Bottlenecks are the primary culprits behind reduced efficiency. Common bottlenecks in pipe bundling operations include:
- Manual feeding: Relying on manual labor for feeding pipes into the machine can be slow and inconsistent.
- Alignment issues: Misaligned pipes can lead to bundling errors and machine downtime.
- Slow strapping: Inefficient strapping mechanisms can significantly reduce overall throughput.
- Ejection delays: Delays in ejecting completed bundles can create backups and halt production.
1.3 Implementing Targeted Solutions
Once you’ve identified the bottlenecks, you can implement targeted solutions to address them. These solutions might include:
- Automation upgrades: Consider adding automated feeding or alignment systems to reduce manual labor and improve consistency.
- Strapping mechanism improvements: Upgrade to a faster, more reliable strapping mechanism to increase bundling speed.
- Workflow optimization: Rearrange the workflow to minimize material handling and movement.
1.4 Data-Driven Optimization
Collecting and analyzing data is crucial for continuous improvement. Track key metrics such as:
- Bundling speed: The number of bundles completed per hour.
- Downtime: The amount of time the machine is out of operation due to maintenance or repairs.
- Material waste: The amount of strapping material wasted per bundle.
- Error rate: The number of bundles that are rejected due to errors.
Use this data to identify trends and areas where further optimization is needed.
1.5 The Power of Preventative Maintenance
Preventative maintenance is key to minimizing downtime and maximizing machine lifespan. Implement a regular maintenance schedule that includes:
- Lubrication: Regularly lubricate moving parts to reduce friction and wear.
- Inspection: Inspect belts, pulleys, and other components for wear and tear.
- Cleaning: Keep the machine clean and free of debris to prevent malfunctions.
- Calibration: Calibrate sensors and other components to ensure accurate operation.
1.6 Operator Training
Proper operator training is crucial for ensuring efficient and safe machine operation. Train operators on:
- Machine operation: How to properly operate the machine and its various functions.
- Troubleshooting: How to identify and resolve common problems.
- Maintenance: How to perform basic maintenance tasks.
- Safety: How to operate the machine safely and avoid accidents.
By carefully analyzing your current workflow, identifying bottlenecks, implementing targeted solutions, and investing in preventative maintenance and operator training, you can significantly improve your pipe bundling machine efficiency in a low-cost operation.
Here’s a table summarizing the key aspects of workflow optimization:
Aspect | Description | Benefits |
---|---|---|
Workflow Analysis | Meticulously map the current pipe bundling process, from feeding to ejection. | Identify inefficiencies and bottlenecks. |
Bottleneck Detection | Pinpoint areas causing delays: manual feeding, alignment issues, slow strapping, and ejection delays. | Allows for targeted solutions to address specific issues. |
Targeted Solutions | Implement automation upgrades, improve strapping mechanisms, and optimize workflow. | Reduces manual labor, improves consistency, and increases bundling speed. |
Data-Driven Approach | Track bundling speed, downtime, material waste, and error rates. | Provides insights for continuous improvement and identifies trends. |
Preventative Maintenance | Regular lubrication, inspection, cleaning, and calibration. | Minimizes downtime, maximizes machine lifespan, and prevents malfunctions. |
Operator Training | Training operators on machine operation, troubleshooting, maintenance, and safety protocols. | Ensures efficient and safe machine operation, reduces errors, and empowers operators to handle basic maintenance tasks. |
2. Cost-Effective Upgrades for Pipe Bundling Machines
Upgrading doesn’t always mean a hefty investment. Explore affordable enhancements that can significantly boost your machine’s performance.
Cost-effective upgrades for pipe bundling machines include adding automated feeding systems, upgrading to more efficient strapping mechanisms, and implementing smart sensor technology. These upgrades can significantly improve throughput and reduce material waste without requiring a complete machine replacement.
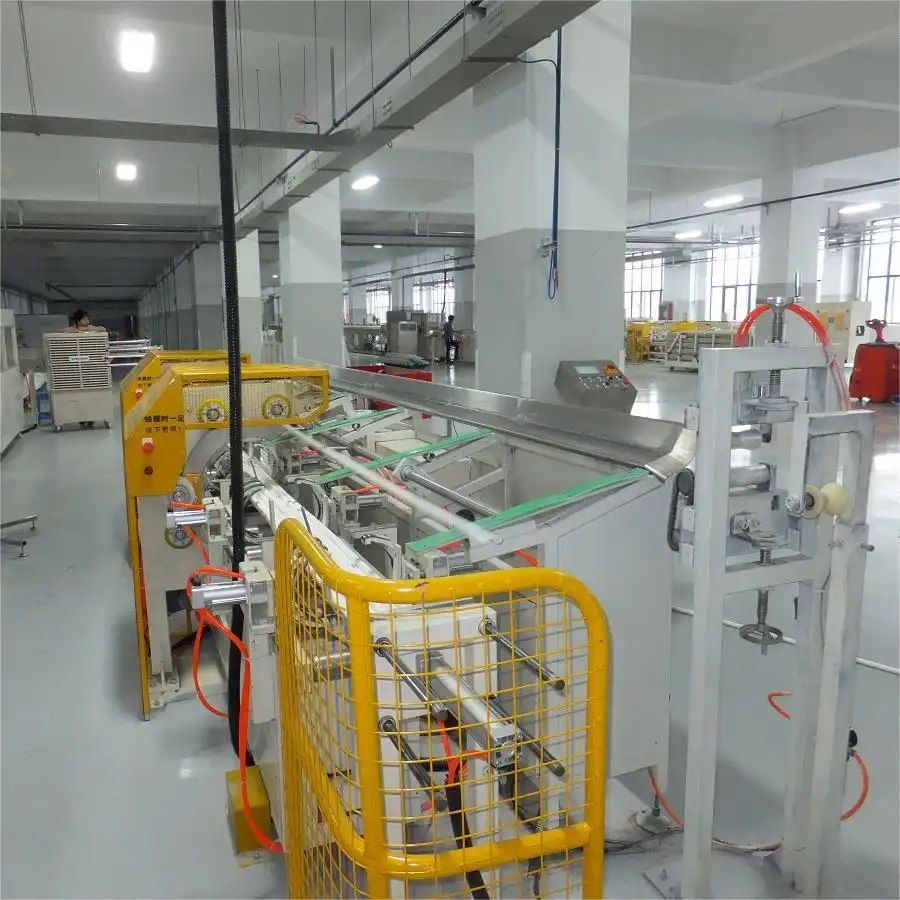
Smart Enhancements: Focusing on Practical Improvements
Boosting performance without overspending is a smart approach. Let’s dive into practical and affordable upgrades for your pipe bundling machine.
Investing in cost-effective upgrades can significantly enhance the low-cost operations of your pipe bundling machine without breaking the bank. By focusing on specific areas, you can achieve substantial improvements in efficiency and reduce operational expenses.
-
Automated Feeding Systems:
- Benefits: Reduces manual labor, ensures consistent pipe feeding, minimizes errors, and increases throughput.
- Considerations: Select a system compatible with your pipe sizes and production volume. Evaluate the system’s reliability and ease of maintenance.
-
Efficient Strapping Mechanisms:
- Benefits: Increases bundling speed, reduces strapping material waste, ensures secure bundling, and minimizes downtime.
- Considerations: Choose a mechanism with adjustable tension settings to accommodate different pipe sizes and materials. Opt for a system with a quick-change dispenser for the strapping material.
-
Smart Sensor Technology:
- Benefits: Improves accuracy, detects errors early, minimizes material waste, and enhances overall efficiency.
- Considerations: Install sensors to monitor pipe alignment, bundle size, and strapping tension. Integrate sensors with the machine’s control system for real-time feedback and adjustments.
By carefully considering these upgrades and selecting the options that best suit your needs, you can significantly improve the efficiency of your pipe bundling machine while keeping costs under control.
3. The Role of Preventative Maintenance in Pipe Bundling Machine Efficiency
Consistent maintenance is the backbone of any efficient operation. Discover how a proactive approach can minimize downtime and maximize your machine’s lifespan.
Preventative maintenance plays a crucial role in pipe bundling machine efficiency by minimizing downtime and extending the machine’s lifespan. Regular lubrication, inspection, and component replacement can prevent costly breakdowns and ensure consistent performance. A well-maintained machine operates more efficiently, reducing waste and maximizing throughput.

Keeping it Running: Implementing a Solid Maintenance Plan
A well-maintained machine is an efficient machine. Let’s explore how to create a preventative maintenance plan for optimal performance.
A well-structured preventative maintenance program is critical for maintaining and improving the efficiency of pipe bundling machine efficiency. It not only minimizes downtime and extends the lifespan of the machine, but also contributes to consistent performance and reduced operational costs.
3.1 Key Elements of a Preventative Maintenance Plan:
- Regular Inspections: Conduct routine inspections of all critical components, including belts, pulleys, sensors, and strapping mechanisms.
- Lubrication: Regularly lubricate moving parts to reduce friction and prevent wear. Use appropriate lubricants recommended by the manufacturer.
- Cleaning: Keep the machine clean and free of debris to ensure smooth operation and prevent malfunctions.
- Component Replacement: Replace worn or damaged components promptly to prevent further damage and maintain optimal performance.
- Calibration: Calibrate sensors and other measuring devices regularly to ensure accuracy.
3.2 Creating a Maintenance Schedule:
Develop a detailed maintenance schedule that outlines the frequency of each maintenance task. Consider factors such as machine usage, operating conditions, and manufacturer recommendations.
3.3 Training Maintenance Personnel:
Ensure that maintenance personnel are properly trained on all aspects of machine maintenance and repair. Provide them with the necessary tools and equipment to perform their tasks effectively.
3.4 Benefits of Preventative Maintenance:
Preventative maintenance offers a wide range of benefits, including:
- Reduced Downtime: Regular maintenance helps prevent breakdowns and reduces the amount of time the machine is out of service.
- Extended Lifespan: Proper maintenance extends the lifespan of the machine, reducing the need for costly replacements.
- Consistent Performance: A well-maintained machine operates more consistently and reliably, ensuring stable output.
- Reduced Operational Costs: Preventative maintenance helps reduce operational costs by minimizing downtime, extending lifespan, and preventing costly repairs.
- Improved Safety: Regular maintenance helps ensure that the machine operates safely, protecting operators and preventing accidents.
By implementing a comprehensive preventative maintenance plan, you can significantly improve the efficiency and reliability of your pipe bundling machine, while also reducing operational costs and improving safety.
Here is a table outlining the benefits of preventative maintenance:
Benefit | Description | Impact on Efficiency |
---|---|---|
Reduced Downtime | Regular maintenance prevents breakdowns and minimizes the time the machine is out of service. | Ensures continuous operation and maximizes throughput. |
Extended Lifespan | Proper maintenance extends the lifespan of the machine, reducing the need for costly replacements. | Reduces long-term costs and ensures a consistent return on investment. |
Consistent Performance | A well-maintained machine operates more consistently and reliably, ensuring stable output. | Minimizes variations in output quality and ensures consistent product standards. |
Reduced Costs | Preventative maintenance reduces operational costs by minimizing downtime, extending lifespan, and preventing repairs. | Lowers overall expenses and improves profitability. |
Improved Safety | Regular maintenance helps ensure that the machine operates safely, protecting operators and preventing accidents. | Creates a safer working environment and reduces the risk of accidents and injuries. |
4. Material Selection for Cost-Effective Pipe Bundling
Choosing the right bundling materials can significantly impact both efficiency and cost. Consider the options carefully.
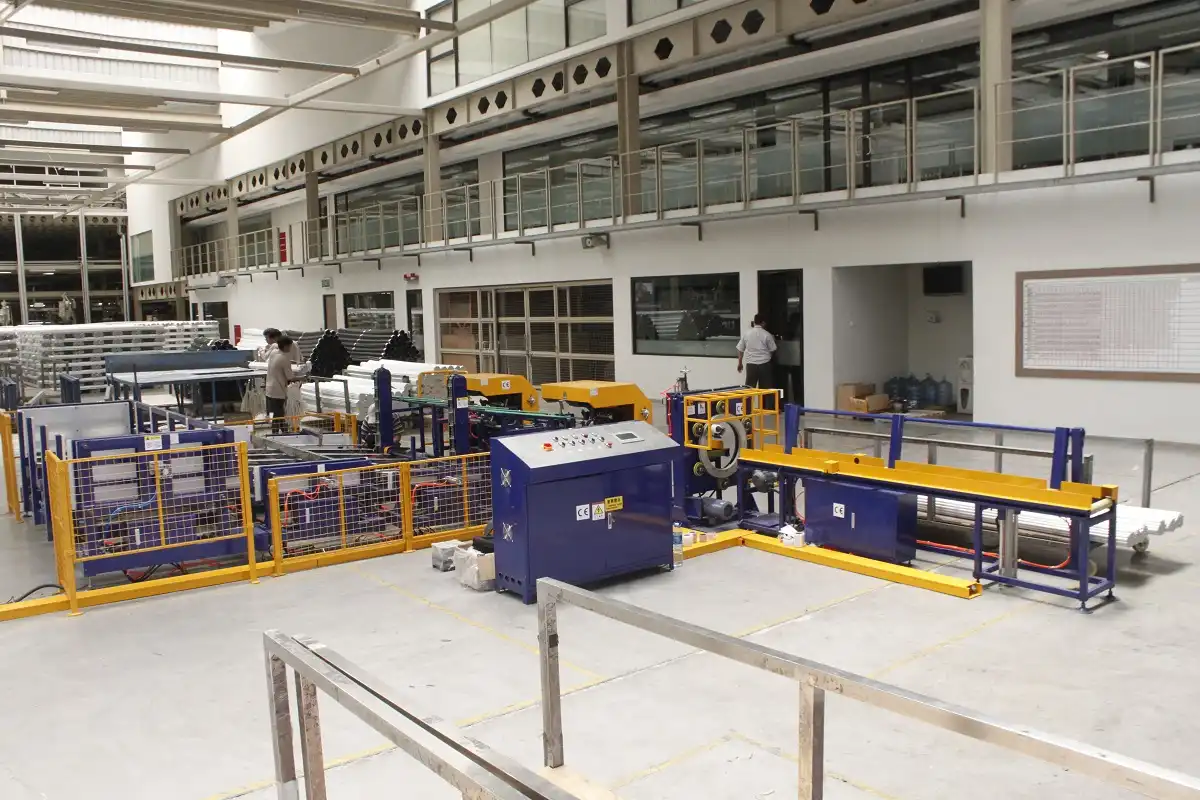
Selecting the right material is crucial for effective and economical pipe bundling. Different materials offer varying degrees of strength, flexibility, and cost-effectiveness. Choosing the right material ensures secure bundling while minimizing waste and expense.
Material selection significantly impacts the efficiency and cost of pipe bundling. Opt for durable yet cost-effective materials like stretch film or polypropylene strapping. Consider factors such as pipe weight, environmental conditions, and transportation requirements. Proper material selection reduces waste, ensures secure bundling, and minimizes material costs.
Efficient low-cost operations depend not only on the machinery, but also on the choice of materials. Consider these points when evaluating materials for bundling:
- Durability: The bundling material should be strong enough to withstand the weight and handling of the pipes.
- Cost: Balance durability with cost-effectiveness.
- Environmental Factors: Consider the environmental conditions the bundled pipes will be exposed to (e.g., moisture, temperature).
- Ease of Use: The material should be easy to apply and remove.
Conclusion
Improving pipe bundling machine efficiency in low-cost operations is achievable through a combination of strategic planning, targeted upgrades, and consistent maintenance. By optimizing existing workflows, implementing affordable enhancements, and prioritizing preventative maintenance, businesses can significantly increase throughput and reduce operational costs. Careful consideration of bundling materials further contributes to efficiency and cost-effectiveness. These strategies empower operations to achieve peak performance within budgetary constraints.