How to Ensure Safety in Plastic Pipe Bundling Operations?
Plastic pipe bundling operations, though essential, present potential security challenges. Prioritizing safety is paramount to ensuring a secure operational environment. By implementing robust measures, we can mitigate risks and ensure the well-being of personnel.
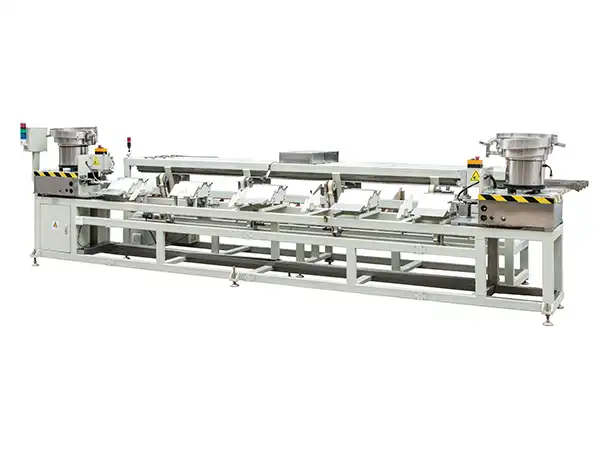
To ensure safety in plastic pipe bundling operations, operators must implement comprehensive safety training, conduct regular risk assessments, maintain equipment meticulously, and adhere to industry standards and legal requirements. This proactive approach will minimize risks and ensure a safe working environment.
Addressing these concerns requires a multifaceted approach. Now, let’s examine the tangible measures and strategies that can substantially enhance safety in plastic pipe bundling operations.
1. Prioritizing Comprehensive Safety Training
A well-trained workforce is crucial in maintaining high security standards. Comprehensive safety training equips employees to identify and address potential risks effectively. This proactive approach minimizes incidents and promotes a safer working environment.
Comprehensive safety training in plastic pipe bundling operations involves detailed manuals, regular drills, hazard identification, and clear communication. Equipping employees with skills and knowledge minimizes risks, fosters vigilance, and creates a safer work environment for all.
But what exactly does comprehensive training entail, and how can it tangibly improve safety outcomes?

Crafting a Robust Training Curriculum
An effective training program should cover multiple critical areas to ensure operators are well-prepared for their roles.
Key Elements of a Comprehensive Program:
-
Machine Operation: Operators must thoroughly understand the functionality of the bundling equipment, including its components, operation cycles, and controls.
-
Safety Protocols: Training must cover safety procedures, including emergency shutdowns, lock-out/tag-out procedures, and proper PPE usage.
-
Hazard Identification: Employees should be trained to recognize potential hazards, such as pinch points, moving parts, and unstable loads.
-
Emergency Response: Protocols for accidents, equipment malfunctions, and other emergencies must be clearly communicated and rehearsed.
-
Ergonomics: Training in proper lifting techniques and ergonomic practices helps prevent injuries during manual handling tasks.
Tailoring Training for Different Roles
To maximize impact, training should be customized for different roles within the bundling operation.
Role Specific Training Focus Machine Operators Operation, safety protocols, emergency shutdowns, basic troubleshooting Supervisors Safety oversight, incident investigation, hazard assessment, enforcement of protocols Maintenance Staff Advanced troubleshooting, equipment repair, safety interlock maintenance, complex diagnostics Incorporating Diverse Training Methods
A variety of training methods can enhance comprehension and retention.
-
Classroom Sessions: Lectures and presentations on safety theory, equipment operation, and regulatory compliance.
-
Hands-On Training: Supervised practice on the equipment to simulate real-world scenarios and reinforce procedures.
-
Visual Aids: Use of diagrams, videos, and simulations to illustrate concepts and demonstrate best practices.
-
Regular Drills: Simulated emergency scenarios to practice response protocols and reinforce awareness.
Reinforcing Continuous Learning
Training should be an ongoing process, not a one-time event. Regular refresher courses, updates on new safety technologies, and incident reviews help keep security awareness at the forefront. [Plastic pipe bundling safety] is an integral component that needs to be emphasized at all times.
2. Implementing Advanced Equipment Safeguards
Advanced equipment safeguards protect operators from potential hazards. By using state-of-the-art safety devices, the bundling operations’ security enhances considerably.
Implementing advanced equipment safeguards involves installing light curtains, safety interlocks, emergency stops, and comprehensive guarding. Regular inspections and maintenance ensure these measures function correctly, minimizing risks and protecting workers.
Which safety devices are available? How do they function to prevent accidents?
Plastic pipe bundling safety, operational guidelines, pipe packaging machines Essential Equipment Safeguards
Key elements to consider include:
-
Light Curtains: Install light curtains around hazardous areas. These stop the machinery when a light beam is interrupted, preventing accidental access.
-
Safety Interlocks: Use safety interlocks on access doors and guards. These ensure the equipment cannot operate unless all safety barriers are properly in place.
-
Emergency Stop Buttons: Place easily accessible emergency stop buttons at strategic points. These enable immediate shutdowns during critical situations.
-
Comprehensive Guarding: Use physical barriers to restrict access and prevent contact with moving parts.
Safety Device Functionality Light Curtains Immediate shutdown when light beam is interrupted, preventing accidental access to dangerous areas Safety Interlocks Prevents operation unless safety guards/doors are correctly positioned and closed Emergency Stop Buttons Provides an easy and quick way to halt all machine operations during emergencies Comprehensive Guarding Physical barriers restrict access and prevent contact with moving parts Enhance Equipment and Machine Integration
To maximize the impact of safety devices, integrate them seamlessly with the bundling equipment. This includes regular inspections, functional testing, and maintenance. Employ sensors to monitor machine vibration and temperatures, enabling proactive troubleshooting and preventive maintenance. Additionally, implement automated shutdown systems that halt operation if anomalies are detected, minimizing the risk of accidents.
3. Establishing Clear [Operational Guidelines] (https://www.fhopepack.com/Plastic-Pipe-Packing-Line/)
Clear and understandable operational guidelines are critical for maintaining a consistent and secure environment. These provide structure and minimize the potential for errors.
Establishing clear operational guidelines involves creating detailed standard operating procedures (SOPs), ensuring clear communication and easy accessibility. Regular reviews and updates maintain relevance, enhancing security and operational consistency.
But what should these operational guidelines include, and how can they be effectively implemented and maintained?

Detailed Steps in Creating Operational Guidelines
Detailed operational guidelines should cover every aspect of the bundling process, from startup to shutdown.
Essential Components:
-
Startup Procedures: Clear, step-by-step instructions for starting the equipment, including pre-operation checks and system initialization.
-
Operational Protocols: Standard operating procedures (SOPs) for handling different pipe sizes, bundling parameters, and material types.
-
Shutdown Procedures: Clearly defined processes for normal and emergency shutdowns, ensuring equipment is safely powered down.
-
Emergency Response: Protocols for responding to equipment malfunctions, accidents, and other emergencies, including evacuation and first aid procedures.
Best Practices for Effective Implementation:
-
Use Simple Language: Guidelines should be written in clear, concise language, avoiding technical jargon.
-
Incorporate Visuals: Diagrams, illustrations, and videos enhance understanding and demonstrate procedures.
-
Involve Operators: Engage operators in the development of guidelines to ensure they are practical and easy to follow.
-
Accessibility: Provide guidelines in multiple formats (printed manuals, digital files) and ensure they are readily available at workstations.
Here’s a schedule for Regular Review and Updating:
Guideline Aspect Review Frequency Update Triggers Safety Procedures Quarterly New regulations, incident reports, equipment modifications Operational Protocols Annually Changes in materials, product specifications, or optimization of processes Emergency Response Bi-Annually Modifications to emergency plans, changes in contact personnel, improvements to drills 4. The Role of Risk Assessment in Ensuring Safety
Risk assessment is a proactive process that involves identifying and evaluating potential hazards associated with [pipe packaging machines]. By conducting regular risk assessments, employers can develop effective strategies for mitigating risks and ensuring a safe working environment.
compliance guidelines
Risk assessment involves identification, evaluation, and mitigation. Regular assessments help pinpoint hazards and implement controls to ensure a safer workplace. A safe environment enhances productivity and reduces the likelihood of costly incidents, benefiting both employees and the organization.
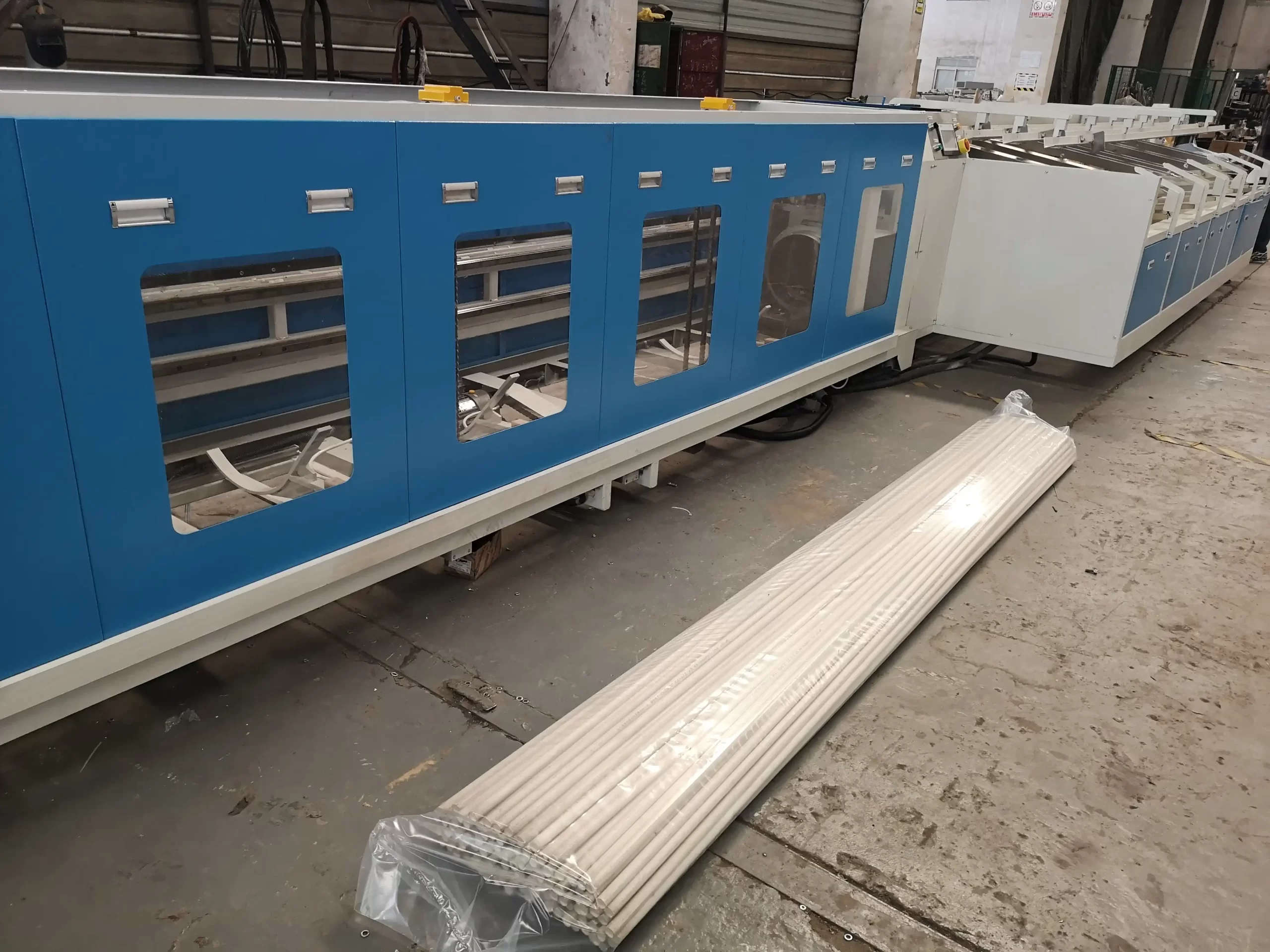
Essential Elements of Risk Assessment include :
- Hazard Identification: A systematic process to identify potential sources of harm, including equipment malfunctions, unsafe behaviors, and environmental factors.
- Risk Analysis: Evaluating the probability and potential severity of each identified hazard, prioritizing those that pose the greatest risk.
- Control Measures: Implementing strategies to eliminate or minimize risks, such as engineering controls, administrative procedures, and personal protective equipment (PPE).
- Documentation: Maintaining detailed records of risk assessments, findings, and corrective actions to ensure accountability and continuous improvement.
-
Performing Regular Audits: To ensure sustained security, conduct audits on a regular basis.
- Establish audit schedules for ongoing assessments.
- Assess process and procedure compliance.
- Address and update findings.
- Sustain process efficiency.
Integrating Operator Feedback is key, by:
- Encouraging feedback from line operators.
- Evaluating suggestions for new processes.
- Creating and implementing new ideas and processes.
The following is an example of a Risk Matrix:
Hazard Likelihood Severity Risk Level Control Measures Entanglement Moderate High High Install machine guards, provide safety training, implement lockout/tagout procedures Electrical Shock Low High Medium Inspect electrical components, ensure proper grounding, provide insulated tools Ergonomic Stressors High Moderate Medium Adjust workstation height, provide ergonomic training, encourage regular breaks Slips and Falls Moderate Low Low Maintain clean and dry floors, provide non-slip footwear, implement housekeeping procedures Conclusion
Ensuring compliance with safety regulations for pipe bundling machines is not merely a matter of following rules; it is about creating a culture of safety that protects workers, promotes operational efficiency, and safeguards the company’s reputation. By understanding the key safety regulations, implementing comprehensive safety measures, and conducting regular risk assessments, employers can create a safer and more productive working environment.