How to Ensure Compliance with Safety Regulations for Steel Wire Strapping Machines?
Steel wire strapping machines are vital in various industries, enhancing efficiency and security. However, ensuring their safe operation is paramount to protect personnel and prevent accidents. Compliance with safety regulations is not just a legal obligation but a moral imperative.
To ensure compliance with safety regulations for steel wire strapping machines, implement regular inspections, provide comprehensive training, use appropriate PPE, and adhere to manufacturer guidelines. Maintaining a safe operational environment is crucial for preventing accidents and ensuring regulatory compliance.
The following detailed guidelines aim to assist you in achieving a compliant and safe operational environment, thereby minimizing risks and maximizing efficiency. Let’s dive deeper into the critical aspects of compliance.
1. Comprehensive Training and Education Programs
Providing thorough training is the bedrock of safety when operating steel wire strapping machines. Untrained personnel can pose a significant risk to themselves and others. A well-structured training program ensures operators are competent and aware of potential hazards.
Comprehensive training for steel wire strapping machine operators should cover machine operation, safety protocols, emergency procedures, and proper maintenance. Regular refresher courses are essential to reinforce knowledge and address evolving safety standards, ensuring consistent and safe operation.
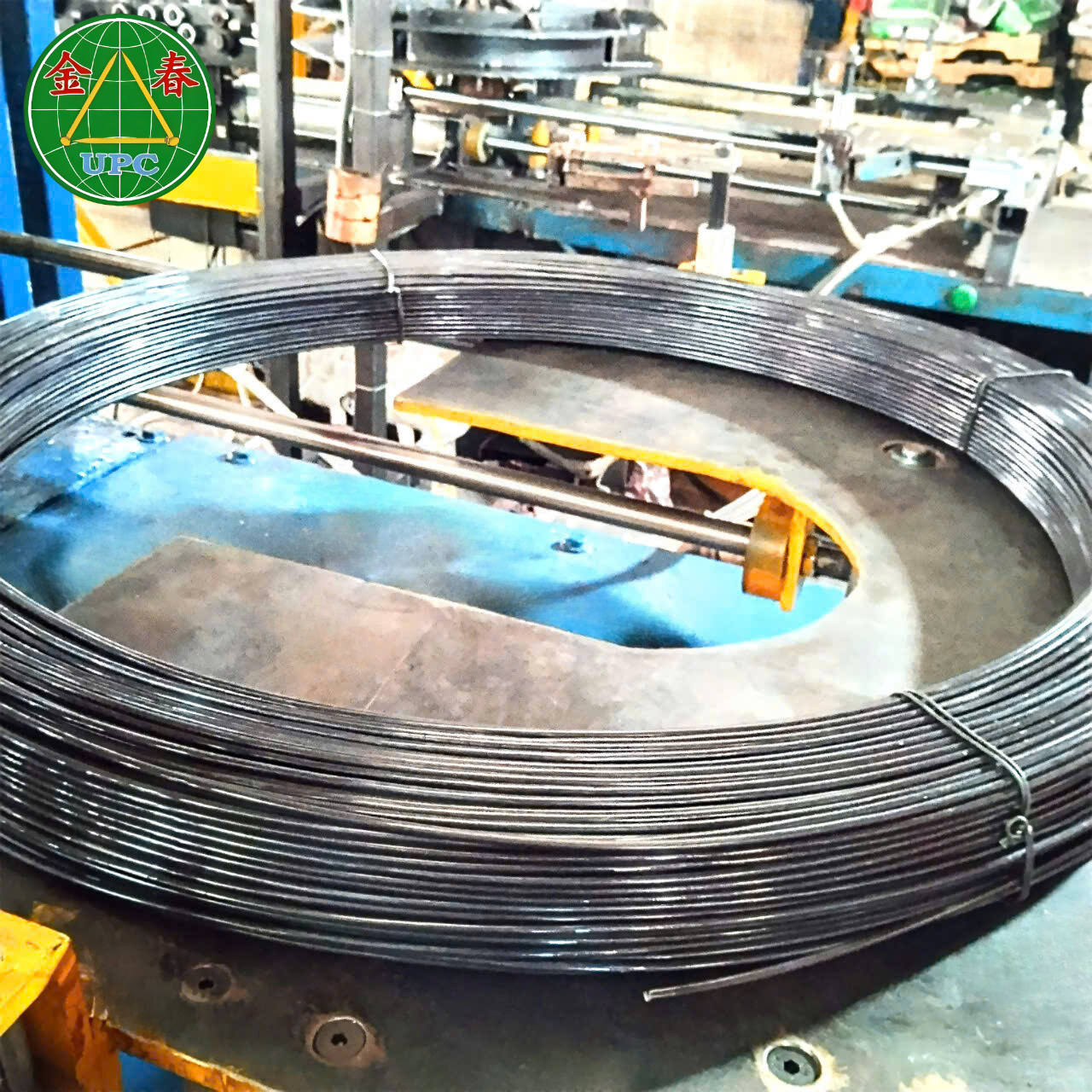
The Key Components of Effective Training
Effective training programs should encompass both theoretical knowledge and hands-on experience. Breaking down the training into manageable modules can improve comprehension and retention. Here’s a closer look at the essential training components:
1. Machine Operation and Functionality
Operators must understand the machine’s components, controls, and operational principles. This includes:
- Control Panel Familiarization: Understanding each button, switch, and indicator light.
- Loading and Unloading Procedures: Knowing the correct methods for loading and unloading materials.
- Adjusting Tension Settings: Learning how to adjust tension to suit different load types.
- Troubleshooting: Recognizing common issues and knowing how to address them.
2. Safety Protocols and Emergency Procedures
Safety training must cover all potential hazards and the necessary precautions to mitigate them. Key elements include:
- Emergency Stop Procedures: Knowing how to quickly stop the machine in case of an emergency.
- Lockout/Tagout Procedures: Understanding how to safely shut down and isolate the machine for maintenance.
- Personal Protective Equipment (PPE): Knowing which PPE is required and how to use it properly.
- Hazard Identification: Recognizing potential hazards such as pinch points, sharp edges, and moving parts.
- First Aid and Emergency Response: Basic first aid knowledge and emergency contact procedures.
3. Maintenance and Inspection Procedures
Regular maintenance is essential for safe operation. Operators should be trained to perform basic maintenance tasks and inspections, including:
- Daily Inspections: Checking for loose parts, damaged components, and proper lubrication.
- Cleaning: Removing debris and keeping the machine clean to prevent malfunctions.
- Lubrication: Applying lubricants to moving parts to reduce friction and wear.
- Reporting Issues: Knowing how to report any issues or concerns to maintenance personnel.
4. Legal and Regulatory Compliance
Operators should be aware of relevant safety regulations and standards, such as those set by OSHA (Occupational Safety and Health Administration) or other local regulatory bodies. This ensures that operations are not only safe but also compliant with legal requirements.
Integrating Practical Training
Theoretical knowledge must be complemented with hands-on training. Practical sessions should include:
- Simulated Operations: Practicing operating the machine under different scenarios.
- Supervised Tasks: Performing actual strapping tasks under the supervision of a qualified trainer.
- Troubleshooting Exercises: Solving simulated machine malfunctions to improve problem-solving skills.
Benefits of Comprehensive Training
Investing in thorough training programs yields significant benefits:
- Reduced Accidents: Well-trained operators are less likely to make mistakes that lead to accidents.
- Increased Efficiency: Competent operators can perform tasks more quickly and effectively.
- Improved Product Quality: Proper strapping techniques ensure products are securely packaged, reducing the risk of damage during transit.
- Enhanced Employee Morale: Employees who feel well-trained and safe are more motivated and productive.
- Compliance Assurance: Regular training ensures that operations meet regulatory requirements, reducing the risk of fines and legal issues.
By prioritizing comprehensive training and education programs, businesses can create a safer, more efficient, and compliant work environment when using steel wire strapping machines.
2. Mandatory Use of Personal Protective Equipment (PPE)
Consistent use of appropriate operational safety is crucial for minimizing the risk of injuries during strapping operations. PPE acts as a barrier between the operator and potential hazards, providing an essential layer of protection.
Mandatory PPE for steel wire strapping machine operators includes safety glasses, gloves, and steel-toed boots. These items protect against common hazards such as flying debris, sharp edges, and falling objects, significantly reducing the risk of workplace injuries and ensuring a safer operational environment.

Detailed Look at Essential PPE
Selecting the right PPE and ensuring its proper use is paramount for operator safety. Here’s a breakdown of essential PPE items:
1. Safety Glasses
Safety glasses are vital for protecting the eyes from flying debris, such as wire fragments or strap particles, which can cause serious eye injuries.
- ANSI Standards: Ensure safety glasses meet ANSI Z87.1 standards for impact resistance.
- Proper Fit: Safety glasses should fit snugly and comfortably to provide adequate protection.
- Regular Inspection: Inspect safety glasses regularly for scratches, cracks, or other damage that could compromise their effectiveness.
2. Gloves
Gloves protect hands from cuts, abrasions, and punctures that can occur when handling steel wire straps.
- Material: Leather or cut-resistant gloves are ideal for providing a balance of protection and dexterity.
- Fit: Gloves should fit well to allow for good grip and control of tools.
- Maintenance: Replace gloves that show signs of wear or damage.
3. Steel-Toed Boots
Steel-toed boots protect feet from falling objects and compression injuries, which are common in industrial environments.
- ANSI Standards: Ensure steel-toed boots meet ANSI Z41 standards for impact and compression resistance.
- Proper Fit: Boots should fit comfortably and provide adequate support.
- Condition: Regularly inspect boots for signs of wear or damage to the steel toe cap or sole.
Implementing a PPE Program
To ensure consistent PPE use, consider implementing the following strategies:
- Policy Enforcement: Establish a clear policy requiring PPE use at all times during strapping operations.
- Training: Train employees on the proper use, maintenance, and storage of PPE.
- Accessibility: Make PPE readily available at workstations.
- Regular Audits: Conduct regular audits to ensure compliance with PPE policies.
- Employee Feedback: Encourage employees to provide feedback on PPE comfort and effectiveness.
By prioritizing the mandatory use of appropriate PPE, businesses can significantly reduce the risk of workplace injuries and create a safer environment for their employees.
3. Regular Inspection and Maintenance Schedules
Consistent inspection and maintenance are critical for ensuring the reliable and safe operation of steel wire strapping machines. Neglecting these essential tasks can lead to equipment malfunctions, increased risk of accidents, and costly downtime.
Regular inspection and maintenance schedules for steel wire strapping machines should include daily checks for wear and tear, monthly detailed inspections, and annual comprehensive assessments. Documenting these inspections helps track maintenance and ensures ongoing compliance with safety standards.
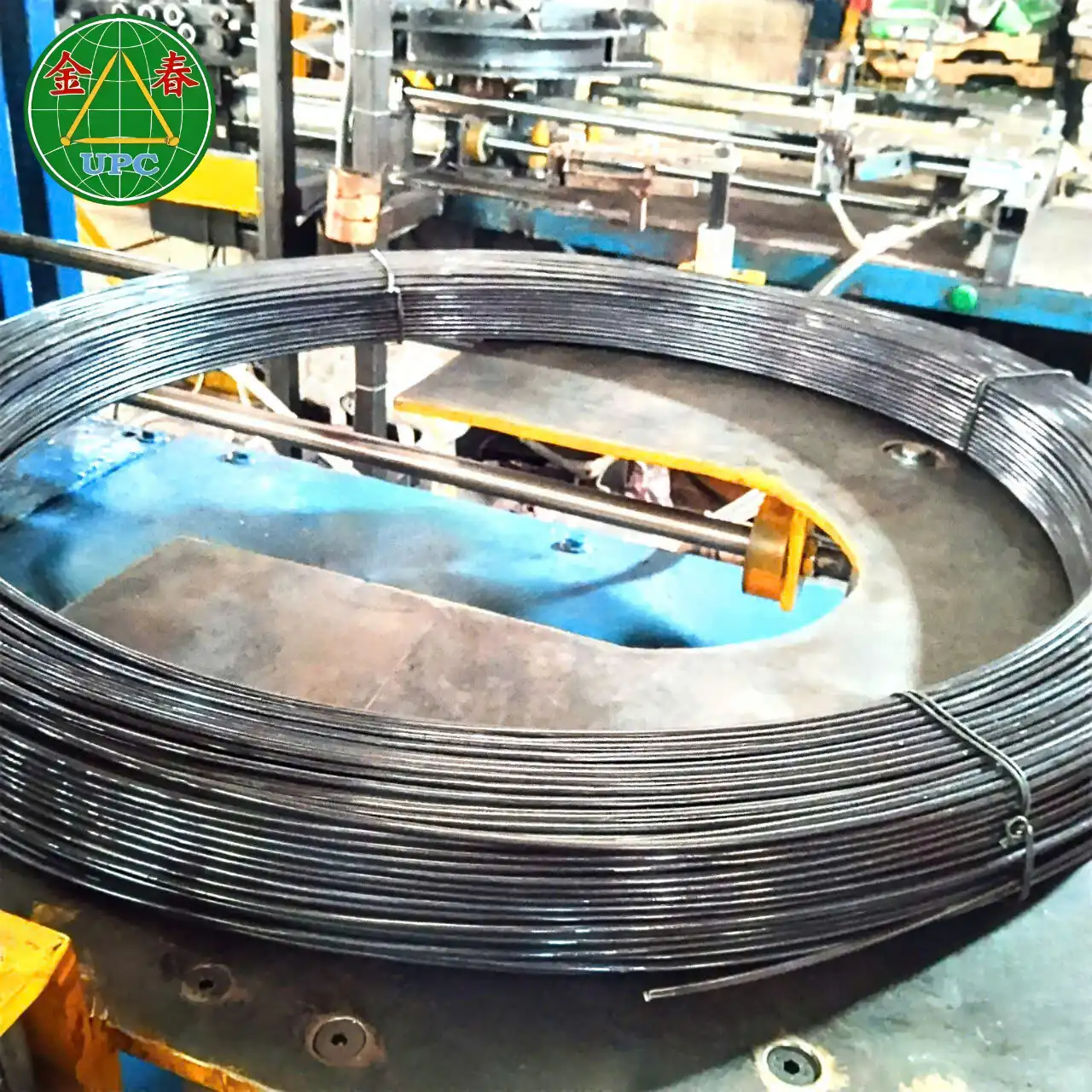
Detailed Breakdown of Inspection and Maintenance
A well-structured inspection and maintenance program encompasses several key areas. Here’s a closer look:
1. Daily Checks
Daily inspections are quick, visual checks performed at the start of each shift. These checks help identify obvious issues that could affect safety or performance. Key areas to inspect include:
- Guards and Safety Devices: Ensure all safety guards and interlocks are in place and functioning correctly.
- Wire Feed Mechanism: Check for any obstructions or damage to the wire feed mechanism.
- Tensioning System: Verify that the tensioning system is working smoothly and accurately.
- Power Cables and Connections: Inspect cables for damage and ensure connections are secure.
- Emergency Stop Buttons: Test emergency stop buttons to ensure they function properly.
2. Monthly Detailed Inspections
Monthly inspections are more thorough and involve a closer examination of the machine’s components. Key areas to inspect include:
- Wear and Tear: Check for worn or damaged parts, such as gears, belts, and bearings.
- Lubrication: Ensure all moving parts are properly lubricated.
- Fasteners: Tighten any loose bolts, screws, or other fasteners.
- Electrical Components: Inspect electrical wiring, switches, and controls for damage or corrosion.
- Calibration: Calibrate the tensioning system to ensure accurate strapping.
3. Annual Comprehensive Assessments
Annual assessments are in-depth inspections performed by qualified technicians. These assessments involve a complete overhaul of the machine and include:
- Detailed Component Inspection: Thoroughly examine all components for wear, damage, or fatigue.
- Performance Testing: Conduct performance tests to verify that the machine meets manufacturer specifications.
- Safety System Evaluation: Evaluate the effectiveness of all safety systems, including guards, interlocks, and emergency stops.
- Software and Firmware Updates: Update software and firmware to ensure optimal performance and security.
- Documentation: Maintain detailed records of all inspections, maintenance, and repairs.
Sample Inspection Checklist
The following table provides a sample checklist for conducting regular inspections:
Inspection Item | Frequency | Description |
---|---|---|
Safety Guards | Daily | Ensure all guards are in place and functioning correctly. |
Wire Feed Mechanism | Daily | Check for obstructions, damage, or wear. |
Tensioning System | Daily | Verify that the tensioning system is working smoothly and accurately. |
Power Cables and Connections | Daily | Inspect for damage and ensure connections are secure. |
Emergency Stop Buttons | Daily | Test to ensure they function properly. |
Lubrication | Monthly | Ensure all moving parts are properly lubricated. |
Fasteners | Monthly | Tighten any loose bolts, screws, or other fasteners. |
Electrical Components | Monthly | Inspect wiring, switches, and controls for damage or corrosion. |
Calibration | Monthly | Calibrate the tensioning system for accuracy. |
Component Inspection | Annual | Thoroughly examine all components for wear, damage, or fatigue. |
Performance Testing | Annual | Verify that the machine meets manufacturer specifications. |
Safety System Evaluation | Annual | Evaluate the effectiveness of safety systems. |
Software Updates | Annual | Update software and firmware to ensure optimal performance and security. |
Benefits of Regular Inspection and Maintenance
- Reduced Downtime: Regular maintenance prevents breakdowns and extends the machine’s lifespan.
- Improved Safety: Consistent inspections identify and address potential hazards, reducing the risk of accidents.
- Enhanced Efficiency: Well-maintained machines operate more smoothly and efficiently, improving productivity.
- Compliance Assurance: Regular inspections ensure that operations meet safety regulations and standards.
- Cost Savings: Preventive maintenance is more cost-effective than emergency repairs.
By establishing and adhering to a rigorous inspection and maintenance schedule, businesses can ensure the reliable, safe, and efficient operation of their steel wire strapping machines.
4. Adherence to Manufacturer Guidelines and Specifications
Following the manufacturer’s guidelines and specifications is paramount for the safe and efficient operation of steel wire strapping machines. These guidelines are developed based on thorough testing and engineering expertise, providing critical information on installation, operation, maintenance, and safety procedures.
To adhere to manufacturer guidelines, operators must consult the equipment’s manual for recommended procedures, safety precautions, and maintenance schedules. Compliance ensures safe, efficient, and prolonged operation, minimizing accidents and maximizing the lifespan of the steel wire strapping machine.

Understanding the importance of compliance with manufacturer guidelines involves several critical steps:
- Comprehensive Review: Read and understand the equipment’s manual thoroughly.
- Training: Ensure that all operators are trained on the manufacturer’s recommended procedures.
- Maintenance: Follow maintenance schedules and procedures.
- Proper Parts: Use only manufacturer-approved parts for repairs and replacements.
- Compliance Checks: Perform regular checks to ensure adherence to all guidelines.
By following these steps, companies can ensure safer and more efficient strapping operations.
Conclusion
Ensuring compliance with safety regulations for steel wire strapping machines is crucial for workplace safety and operational efficiency. Comprehensive training, mandatory PPE, regular maintenance, and adherence to manufacturer guidelines are key components. Prioritizing these measures protects workers, minimizes accidents, and ensures regulatory compliance. Investing in these practices promotes a culture of safety and contributes to the long-term success of the organization.