How to Enhance Security in Steel Wire Coiling Operations?
Steel wire coiling operations present unique safety challenges. Implementing robust security measures is crucial to protect personnel, equipment, and materials. This guide explores key areas to enhance safety and efficiency in these operations.
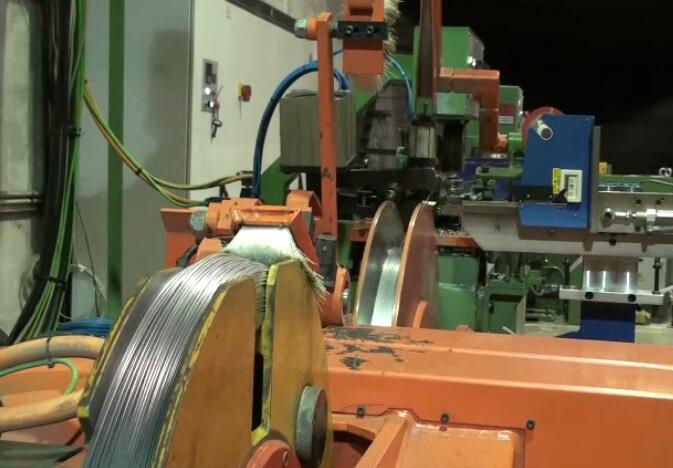
Enhancing security in steel wire coiling involves comprehensive risk assessment, strict adherence to operational guidelines, and robust equipment maintenance. Proper training, use of PPE, and implementing engineering controls like safety barriers and emergency stops are also crucial for preventing accidents and ensuring a safe working environment.
Wire coiling operations can be dangerous if proper safety measures are not implemented. From potential injuries to equipment damage, the risks are real. Let’s delve deeper into specific areas where improvements can significantly reduce these risks and foster a safer working environment.
1: Rope Selection and Pre-Operation Inspection
Selecting the correct rope and conducting thorough pre-operation inspections are crucial first steps for safe steel wire coiling operations. Using the right materials and properly assessing equipment minimizes potential hazards.
Prioritize rope selection by referring to OEM manuals, calculating maximum force, and considering bending fatigue, abrasion, and corrosion. Implement daily inspections focusing on wear, broken wires, and distortion. Regular maintenance ensures equipment functions safely, reducing risk of failure and injury.

The Importance of Material Integrity: A Deep Dive
Beyond the basics, understanding the nuances of rope selection and inspection can dramatically improve safety. Let’s break down key considerations and explore how diligent monitoring can prevent catastrophic failures.
1.1 Understanding Rope Dynamics
Wire rope performance depends on several factors, and choosing the right rope for the job is paramount.
- Bending Fatigue: Continuous bending around sheaves or drums weakens the wire rope, leading to fatigue. Operations involving reverse bending or high speeds demand ropes designed for high bending fatigue resistance.
- Abrasion: Dragging wire rope across abrasive materials or bending it under load causes progressive weakening. Selecting ropes with larger outer wires is beneficial in abrasive environments.
- Corrosion: Ropes with many small wires are more susceptible to corrosion. Regular lubrication or galvanized ropes should be chosen when corrosion is a concern. [Operational guidelines] play a crucial role in mitigating these issues.
1.2 Comprehensive Inspection Protocols
Regular inspections are your frontline defense against potential failures.
- Visual Inspection: Check the entire rope length for signs of wear, broken wires, distortion, and corrosion. Pay close attention to sections entering or leaving grooves on drums and sheaves and areas near terminations.
- Diameter Measurement: Use a rope vernier to measure the diameter. Significant reductions in diameter indicate internal wear or core degradation.
- Internal Inspection: Specialized tools can facilitate internal inspection to detect otherwise invisible fractures or corrosion.
1.3 Balancing Cost and Safety
While cost is always a consideration, prioritizing safety should be non-negotiable.
Factor | Low-Cost Option | High-Quality Option |
---|---|---|
Rope Material | Standard carbon steel | Alloy steel or specialized coatings |
Inspection | Minimal, infrequent checks | Regular, comprehensive inspections with advanced techniques |
Maintenance | Reactive; addressing issues only when they arise | Proactive; scheduled lubrication, cleaning, and component replacement |
Failure Rate | Higher risk of unexpected failures | Lower risk due to enhanced durability and monitoring |
Long-Term Costs | Potentially lower initial cost, higher long-term costs | Higher initial cost, potentially lower long-term costs |
2: Implementing Engineering Controls
Engineering controls involve modifying the physical workspace to reduce or eliminate hazards. These are often the most effective safety measures because they don’t rely on worker behavior.
Install safety barriers around coiling machinery to prevent accidental contact. Implement emergency stop buttons readily accessible to operators. Use automated systems to minimize manual handling of steel wire, reducing the risk of strains and cuts. Regular maintenance of these systems is vital.
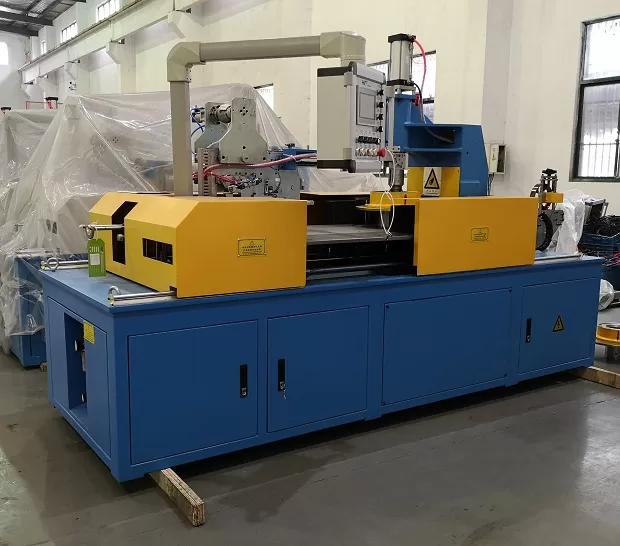
Optimizing Workplace Design for Enhanced Safety
A well-designed workspace can greatly reduce the risk of accidents. Let’s explore key strategies to create a safer environment.
2.1 Safety Barriers and Guarding
Physical barriers are essential for preventing accidental contact with moving machinery.
- Fixed Barriers: Install fixed barriers around the perimeter of coiling machines to restrict access to authorized personnel only.
- Interlocked Guards: Use interlocked guards that automatically shut down the machine when opened, preventing operation during maintenance or inspection.
2.2 Emergency Stop Systems
Easily accessible emergency stop buttons are vital for quickly halting operations in the event of a problem.
- Placement: Position emergency stops near operator stations and potential hazard zones.
- Testing: Regularly test emergency stops to ensure they function correctly.
2.3 Automation and Remote Operation
Automating tasks and operating machinery remotely can significantly reduce worker exposure to hazards.
- Automated Material Handling: Use automated systems to load and unload wire coils, minimizing manual handling.
- Remote Monitoring: Implement remote monitoring systems to allow operators to observe operations from a safe distance.
2.4 Checklist for Engineering Controls
To maximize the effectiveness of these controls, a regular checklist helps ensure optimal functioning.
Control | Check Frequency | Action |
---|---|---|
Safety Barriers | Daily | Inspect for damage; ensure secure attachment |
Emergency Stop Buttons | Weekly | Test functionality; ensure accessibility |
Automated Systems | Monthly | Service and calibrate sensors; check for wear |
Remote Monitoring Equipment | Monthly | Verify signal integrity; check camera placement |
3: Personal Protective Equipment (PPE) and Training
While engineering controls provide a strong foundation, PPE and training are essential for protecting workers from remaining hazards.
Workers must wear industrial gloves to protect against cuts and abrasions from wire. Safety glasses or face shields should be used to prevent eye injuries from flying debris. Steel-toed boots protect feet from falling coils, and proper training on safe coiling practices minimizes risks.

Empowering Workers Through Education and Protection
Providing the right tools and knowledge is essential for creating a safety-conscious workforce. Let’s explore key aspects of PPE and training programs.
3.1 Selecting and Using PPE
The right PPE can make a significant difference in preventing injuries.
- Industrial Gloves: Choose gloves made from cut-resistant materials like Kevlar or Dyneema to protect hands from sharp wire edges.
- Safety Glasses/Face Shields: Select eyewear that meets ANSI Z87.1 standards for impact resistance. Face shields offer additional protection against splashes and debris.
- Steel-Toed Boots: Ensure boots meet ASTM F2413 standards for impact and compression resistance.
3.2 Training Programs
Effective training is critical for ensuring workers understand hazards and how to protect themselves.
- Safe Operating Procedures: Train workers on the correct procedures for operating coiling machinery, including start-up, shut-down, and emergency procedures.
- Hazard Identification: Teach workers to identify potential hazards such as broken wires, loose coils, and equipment malfunctions.
- PPE Usage and Maintenance: Provide training on the proper use, fit, and maintenance of PPE.
3.3 A Culture of Safety
Safety must be more than just rules; it must be a core value.
- Regular Safety Meetings: Hold regular safety meetings to discuss recent incidents, potential hazards, and new safety procedures.
- Employee Feedback: Encourage workers to report safety concerns and provide feedback on safety programs.
- Incentive Programs: Consider implementing incentive programs to reward safe behavior and promote a culture of safety.
4: Regular Equipment Maintenance
Consistent and effective equipment maintenance is essential for maintaining a safe work environment.

Accidents and equipment failure can be avoided by prioritizing regular inspections and maintenance to the coiling equipment.
Establishing a Maintenance Plan
Here’s how to establish a regular inspection and maintenance schedule:
- Regularly inspect all machinery: check for wear and tear.
- Have machinery serviced, replace parts as needed.
- Train employees to flag and immediately resolve damaged equipment.
Equipment | Inspection | Maintenance |
---|---|---|
Coiling machines | Check for wear, loose parts | Lubricate moving parts, replace worn components |
Safety barriers | Inspect for damage | Repair/replace damaged sections |
Emergency stops | Verify functioning | Ensure clear access, fix malfunctions |
PPE | Inspect for damage | Replace worn/damaged equipment |
Conclusion
Enhancing security in steel wire coiling operations requires a multifaceted approach. By prioritizing rope selection, implementing robust engineering controls, providing adequate PPE and training, and maintaining equipment meticulously, companies can create a safer and more efficient working environment. Remember, proactive [risk management] strategies are key to preventing accidents and ensuring long-term success.