How to Enhance Pipe Bundling Machine Performance with Energy-Efficient Designs?
Optimizing pipe bundling machines boosts productivity and reduces operational costs. Energy-efficient designs minimize waste and enhance overall performance. Let’s explore how to improve these essential systems.
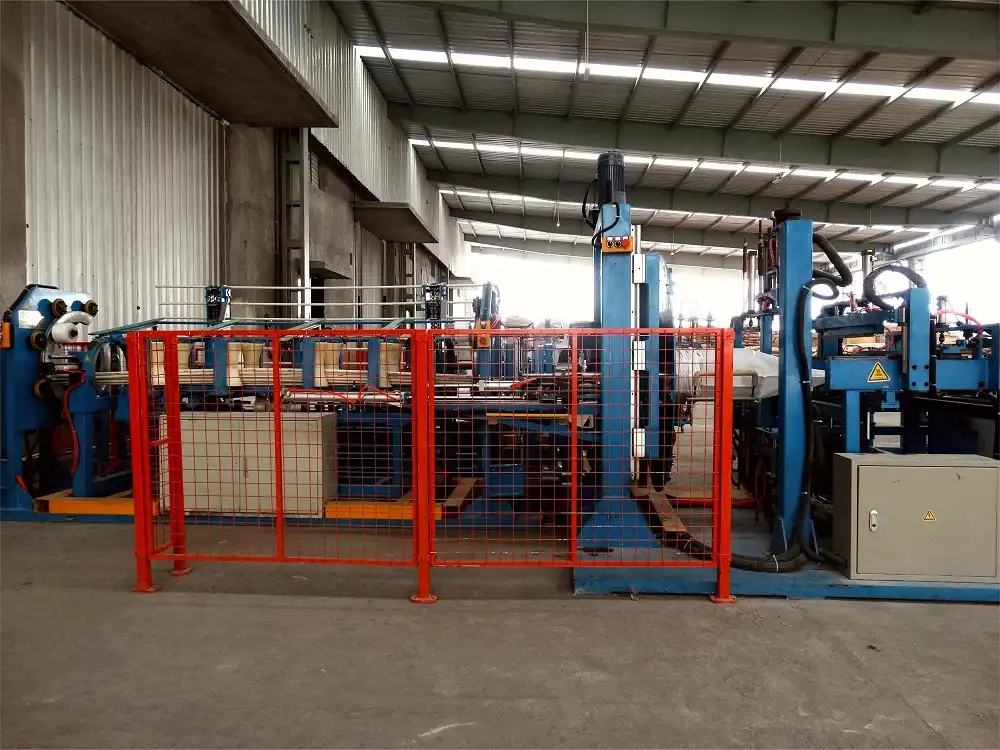
Enhancing pipe bundling machine performance with energy-efficient designs involves integrating servo motors, optimizing sealing, and implementing smart controls. Reducing idle time, using thinner films, and automating processes further minimize energy waste and improve efficiency. These strategies lead to cost savings and environmental benefits.
Modernizing pipe bundling machines can significantly improve efficiency and reduce energy consumption, leading to substantial cost savings and environmental benefits. Ready to delve into the specifics?
1. Optimizing Machine Design for Energy Efficiency
The design of a pipe bundling machine significantly impacts its energy consumption and overall performance. Choosing energy-efficient components and technologies is crucial for creating a sustainable and cost-effective system.
Energy-efficient designs in pipe bundling machines involve incorporating servo motors, optimizing heating and sealing mechanisms, and employing smart control systems. These design choices directly minimize energy waste and improve the machine’s operational efficiency, leading to significant reductions in overall energy consumption. Modern designs also focus on reducing friction and improving material flow.
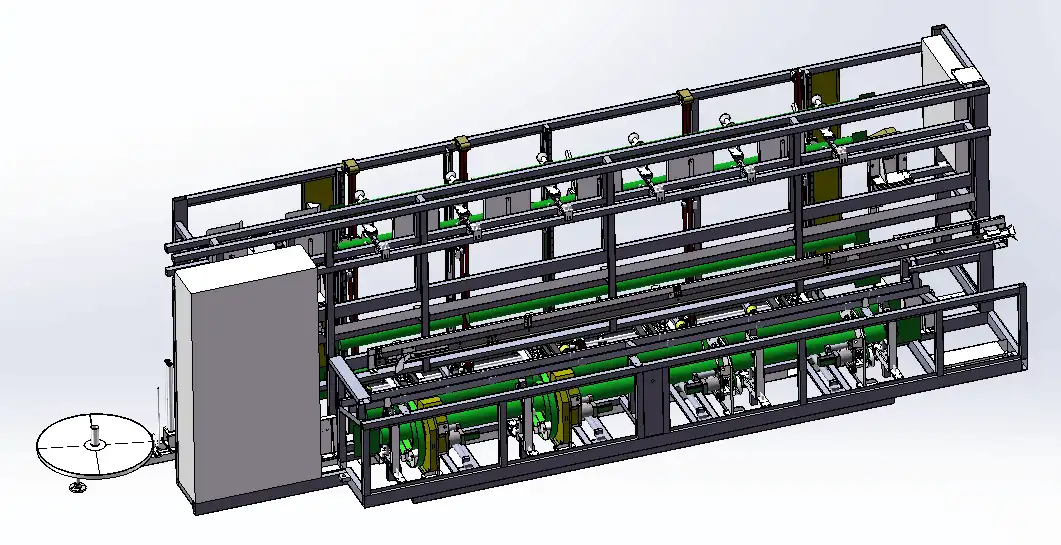
Key Design Elements for Enhanced Energy Savings and Performance
To truly understand how machine design impacts energy consumption, we need to examine specific components and technologies. By focusing on these areas, manufacturers can make informed decisions when selecting or upgrading their pipe bundling equipment.
Servo Motors vs. Traditional Motors: A Comparative Analysis
Servo motors represent a significant advancement in energy efficiency compared to traditional AC motors. Their precision and responsiveness contribute to lower energy consumption, especially during idle periods.
Feature | Traditional AC Motor | Servo Motor | Energy Efficiency Improvement |
---|---|---|---|
Energy Consumption | Higher, even during idle periods | Lower, especially during idle times | Up to 70% |
Control Precision | Less precise, less responsive | Highly precise, rapid response | N/A |
Speed Control | Limited, less flexible | Wide range, highly flexible | N/A |
Heat Generation | Higher, energy loss as heat | Lower, less energy wasted as heat | Significant reduction |
Lifespan | Generally shorter | Generally longer | Longer operational life |
Advanced Sealing Technologies: Cold Sealing vs. Heat Shrink
Traditional heat shrink tunnels are energy-intensive. Cold sealing methods offer a more energy-efficient alternative, reducing energy consumption by up to 90%.
Sealing Technology | Heat Shrink Tunnel | Cold StretchPack Sealing | Energy Consumption Comparison |
---|---|---|---|
Energy Source | High heat generation | Mechanical stretching | Heat shrink uses significantly more energy |
Process | Heat and shrink film | Stretch and seal film | Cold sealing eliminates energy-intensive heating |
Typical Consumption | 150-200 MWh/year | 0.03 kWh per unit | Up to 90% energy saving |
Process Steps | Separate heating and sealing | Combined sealing | Streamlined process reduces energy waste |
Smart Control and Automation Systems: Real-Time Data and Adjustments
Intelligent control systems provide real-time data tracking of motor torque and energy consumption. This allows for targeted optimization and adjustments, ensuring that the machine operates at peak efficiency and minimizes energy waste.
Feature | Benefit | Energy Saving Impact |
---|---|---|
Real-time Data Tracking | Monitors energy usage, identifies high-consumption areas | Allows for targeted optimization and adjustments |
Remote Monitoring & Control | Enables adjustments without physical presence, optimizing settings | Reduces unnecessary machine operation and energy waste |
Automated Adjustments | Programmable sealing controls adapt to production speed | Ensures consistent sealing with minimal energy input |
Parameter Preset Mode | Saves optimal settings for future runs | Reduces setup time and ensures energy-efficient operation |
2. Implementing Smart Operational Strategies
Beyond machine design, how a pipe bundling machine is operated significantly impacts its energy consumption. Implementing smart operational strategies can yield significant energy savings without major equipment upgrades.
Operational energy efficiency in pipe bundling involves practices like reducing machine idle time, optimizing production schedules to avoid peak energy hours, implementing regular maintenance, and training staff on energy-saving procedures. These operational adjustments are crucial for minimizing energy waste in daily machine operation.
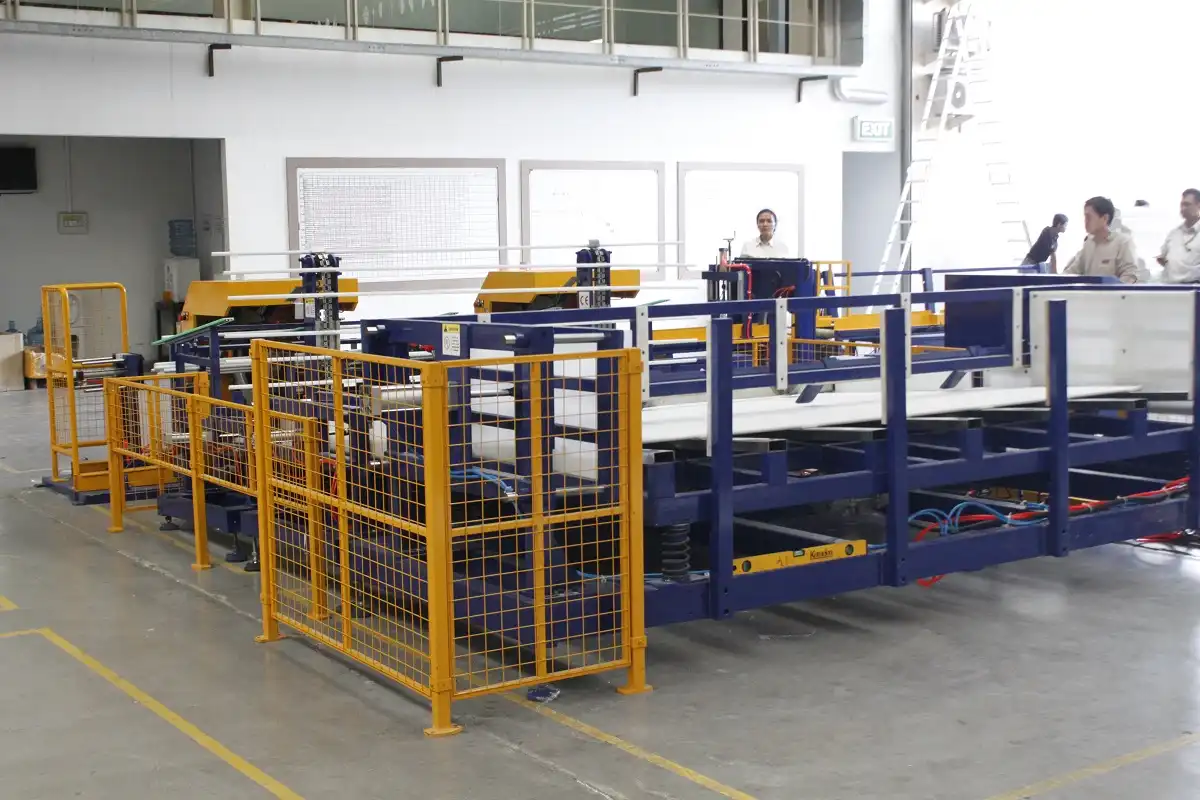
Practical Strategies for Minimizing Energy Use in Daily Operations
Even the most energy-efficient machine can consume excessive energy if not operated optimally. Simple changes in daily operations can dramatically reduce energy consumption.
Optimizing Production Schedules: Shift Operations to Off-Peak Hours
Peak energy demand periods usually come with higher electricity rates. Understanding your facility’s energy consumption patterns and utility rate structures allows you to strategically schedule bundling operations during off-peak hours.
Reducing Idle Time and Standby Consumption: Power Down During Breaks
Pipe bundling machines, like many industrial equipment, can consume energy even when idle. Implementing procedures to power down machines during breaks, shift changes, or periods of inactivity can lead to noticeable energy savings.
Regular Maintenance and Component Checks: Prevent Inefficiencies
Regular maintenance is not just about preventing breakdowns; it’s also about ensuring energy efficiency. Worn or poorly maintained components can lead to increased friction, inefficiencies, and higher energy consumption.
Operator Training and Energy Awareness: Educate Your Staff
Operators are at the forefront of machine operation, and their practices significantly impact energy consumption. Training operators on energy-efficient operation procedures is vital. This includes educating them on the impact of idle time, proper machine startup and shutdown procedures, and recognizing signs of inefficiencies.
3. Material and Process Selection for Lower Energy Bundling
The choice of bundling materials and the bundling process itself can significantly influence the energy footprint of pipe packaging. Selecting materials that require less energy to seal and processes that minimize energy input are key strategies.
Energy-conscious material and process selection for pipe bundling includes opting for thinner yet durable films, choosing materials compatible with cold sealing methods, and optimizing film usage to reduce waste. These choices directly impact the energy needed for sealing and material production, contributing to overall energy reduction.
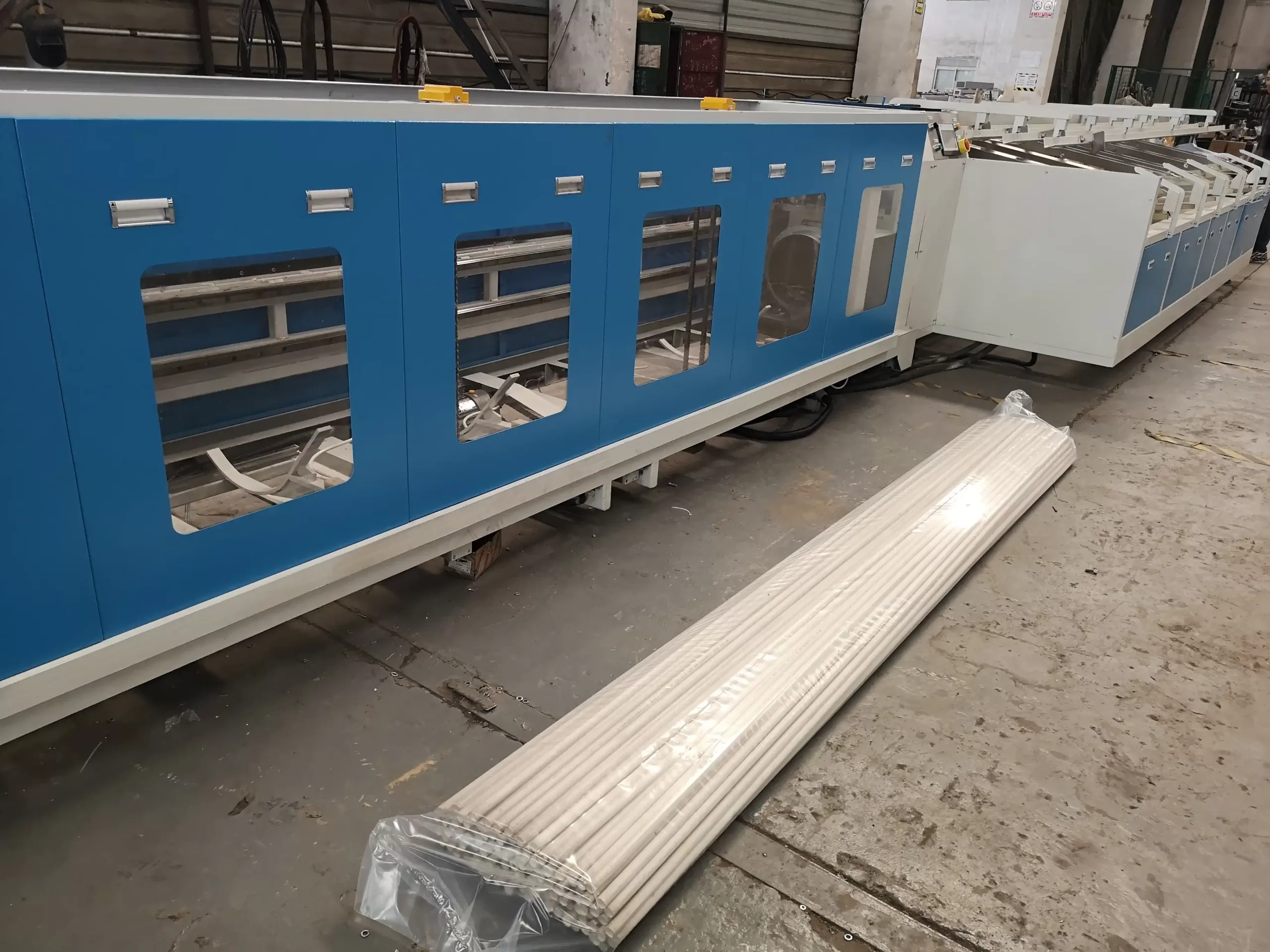
Smart Material Choices and Efficient Processes
The materials used and the processes employed in bundling are not neutral factors in energy consumption. Smart choices in these areas can lead to substantial energy savings.
Choosing Energy-Efficient Bundling Films: Thinner and Recyclable Options
The type of film used for bundling directly impacts energy consumption. Thinner films naturally require less material to produce, reducing the embodied energy. Exploring recyclable and bio-based film options can further reduce the environmental impact.
Optimizing Film Usage and Reducing Waste: Precision Cutting is Key
Minimizing film waste is another way to indirectly reduce energy consumption. Less waste means less material needs to be produced, transported, and potentially disposed of. Precision folding and cutting mechanisms are crucial for optimizing film usage.
Exploring Cold Sealing and Alternative Processes: A Shift from Heat
Cold sealing methods like stretch wrapping offer significant energy advantages over heat shrinking. Exploring alternatives to heat sealing can be beneficial for PVC pipe bundling, where feasible. Pipe packaging technology advancements in cold sealing technologies and film materials may offer viable lower-energy options for specific applications.
Data Table: Material and Process Energy Comparison (Illustrative)
Factor | Traditional Approach (Heat Shrink) | Energy-Efficient Approach (Cold Seal/Optimized Film) | Potential Energy Saving |
---|---|---|---|
Sealing Process | Heat Shrink Tunnel | Cold Stretch Wrapping | Up to 90% |
Film Material | Thicker, Standard Film | Thinner Gauge, Optimized Film (e.g., BOPP) | 10-20% (Material Production) |
Film Waste | Higher Waste Rate | Precision Cutting, Tension Control, Lower Waste | 5-10% (Material & Process) |
Overall Estimated Saving | Baseline | Combined Optimization | Potentially 30-95% |
4. Automation and Integrated Systems for Energy Reduction
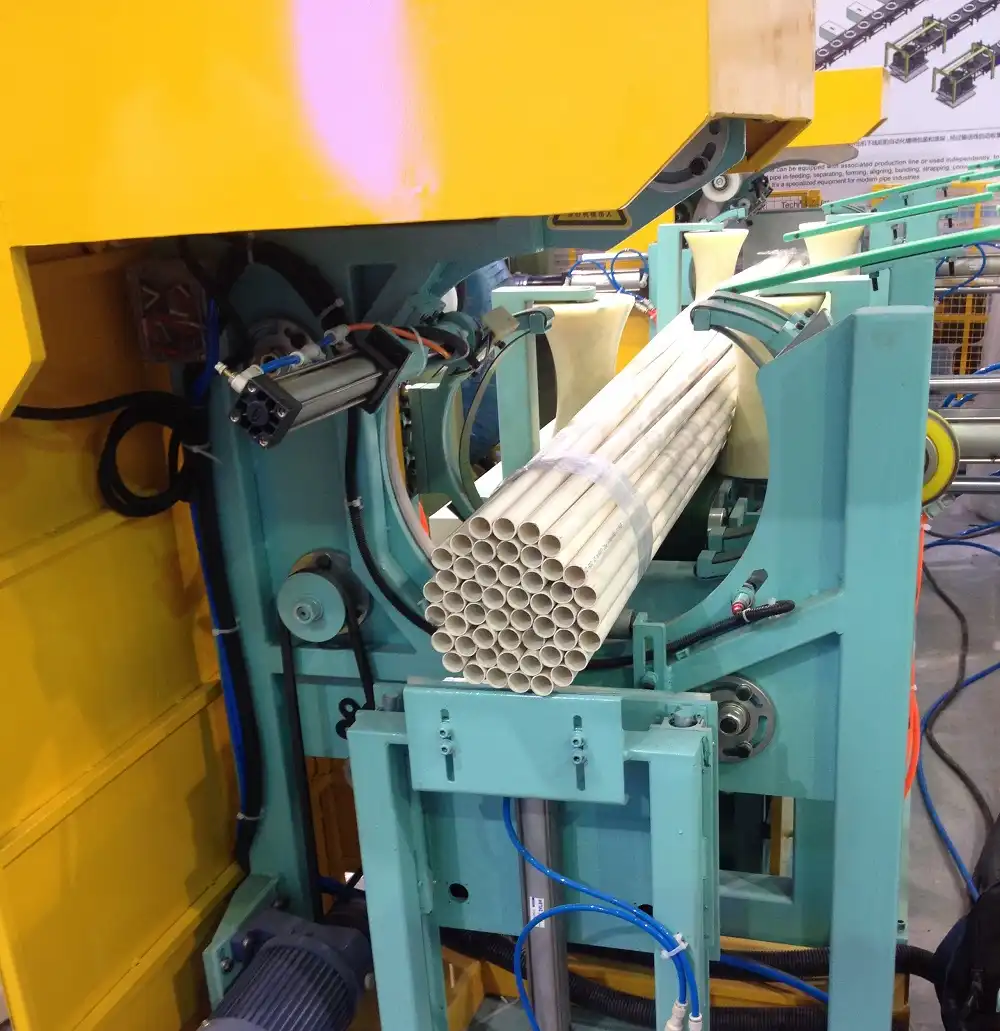
Automation streamlines processes, minimizes manual handling, and optimizes material and energy usage. By strategically implementing energy-efficient technologies, optimizing operations, choosing appropriate materials, and embracing automation, manufacturers can significantly reduce their energy footprint.
Automated bundling lines reduce energy consumption by optimizing material flow, minimizing manual intervention, and ensuring consistent machine operation. Features like automated sealing control, precision servo motors, and integrated systems contribute to significant energy savings and enhanced productivity in PVC pipe packaging processes.
Automated Material Handling and Feeding
Integrated Folding, Sealing, and Cutting
Automated Packaging and Palletizing
Conclusion
Enhancing pipe bundling machine performance through energy-efficient designs is vital for reducing operational costs and environmental impact. Implementing strategies such as servo motors, optimized sealing, and smart controls significantly minimizes energy waste. Embracing automation, optimizing material usage, and promoting energy-conscious practices will improve both sustainability and profitability.