How to Enhance Pipe Bundling Machine Performance with Advanced Sensors?
Ensuring optimal performance of your pipe bundling machine is crucial. Advanced sensors offer a pathway to improve efficiency and minimize downtime. By implementing sensor technology, we can achieve higher productivity and reduce operational costs.
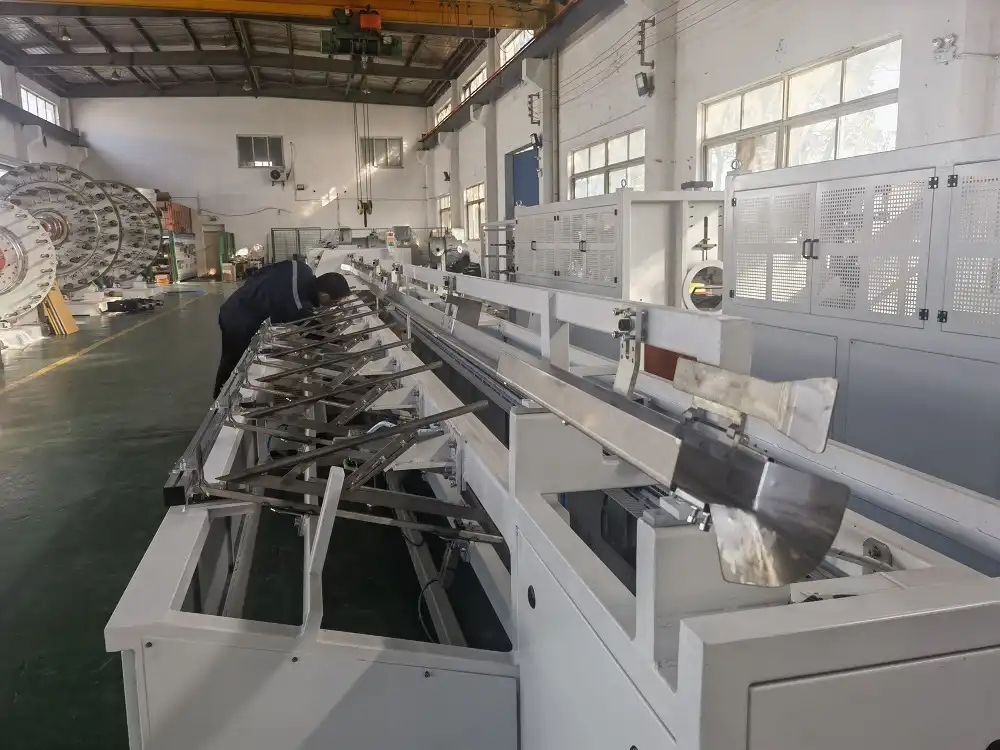
Advanced sensors enhance pipe bundling machine performance by providing real-time data for precise control and proactive maintenance. This minimizes downtime, reduces material waste, ensures consistent bundle quality, optimizes machine lifespan, and improves overall operational efficiency, leading to increased productivity and cost savings.
Ready to delve into how sensors can revolutionize your pipe bundling operations? Let’s explore the specific sensors and how they impact key performance metrics.
1. The Core Role of Sensors in Modern Pipe Bundling Machines
Pipe bundling relies on precision. Advanced sensors offer real-time insights, facilitating immediate adjustments. These sensors enable a shift from reactive to proactive management, increasing overall effectiveness.
Advanced sensors are crucial for real-time monitoring of key parameters in pipe bundling machines, such as tension, speed, and material presence. This allows for immediate adjustments, error detection, and informed decision-making. The result is optimized performance and minimized potential failures, leading to fewer interruptions and consistent output.
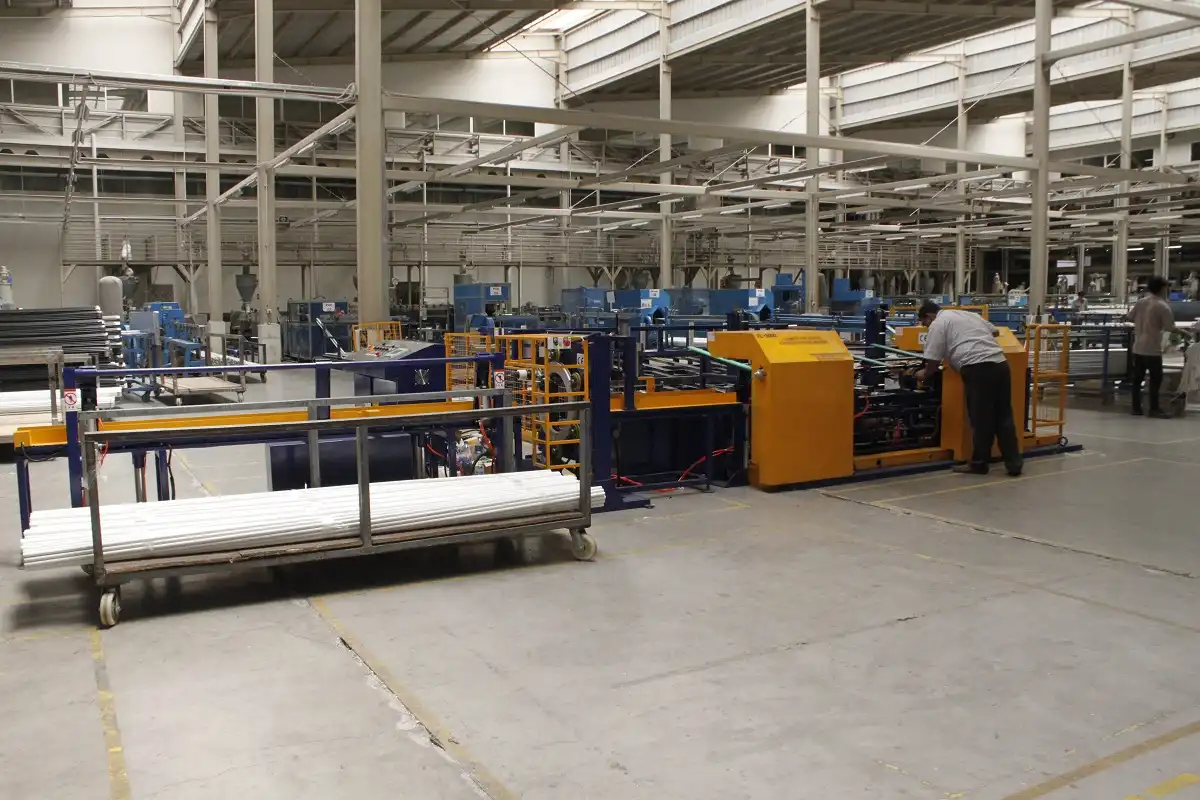
Sensor-Based Monitoring vs. Traditional Methods: A Detailed Analysis
Traditional monitoring methods often involve manual checks and scheduled maintenance. This approach is reactive and inefficient compared to sensor-based monitoring. Let’s examine the specific advantages that sensors bring to the table.
Predictive vs. Preventive vs. Reactive Monitoring: A Comparative Table
The table below highlights the key differences between reactive, preventive, and sensor-based monitoring in pipe bundling machines. Sensor technology provides superior benefits by optimizing performance and reducing downtime.
Feature | Reactive Monitoring | Preventive Monitoring | Sensor-Based Monitoring |
---|---|---|---|
Data Source | None (Post-Failure) | Historical Data, Scheduled Checks | Real-time Sensor Data |
Intervention Timing | After Breakdown | Fixed Intervals | Based on Real-Time Condition |
Downtime Impact | Highest (Unplanned) | Medium (Planned) | Lowest (Optimized) |
Waste Reduction | Least Efficient | Moderate Efficiency | Most Efficient |
Suitability | Simple Machines | Machines with Known Wear | Complex, Critical Machines |
This comparison illustrates the advantages of sensor-based monitoring, particularly for intricate systems like pipe bundling machines. By transitioning from reactive or preventive to sensor-driven predictive maintenance, manufacturers can significantly boost operational efficiency and minimize costly downtime. Embracing this proactive approach ensures a more streamlined and profitable operation.
Deep Dive: Real-World Impact of Sensor Monitoring
To truly appreciate the impact, let’s delve into real-world examples. Imagine a scenario where a tension sensor detects irregularities in the strapping process. A traditional system would only recognize the issue after a bundle fails, leading to material waste and downtime.
With sensor-based monitoring, the system can immediately adjust the tension, preventing the failure altogether. This real-time correction not only saves materials but also ensures consistent bundle quality. Moreover, by tracking vibration patterns, sensors can predict potential mechanical issues before they lead to costly breakdowns.
Consider the implications for overall productivity. By minimizing downtime and reducing waste, manufacturers can significantly increase output. This translates to higher profitability and a more competitive edge in the market. Furthermore, the data gathered by sensors can be used to optimize machine settings, further enhancing performance.
In essence, sensor-based monitoring transforms pipe bundling from a reactive process to a proactive one. This shift empowers manufacturers to make informed decisions, minimize disruptions, and maximize the efficiency of their operations. It’s a fundamental change that drives improved performance across the board.
2. Essential Types of Advanced Sensors for Pipe Bundling
Selecting the right sensors is key to maximizing the benefits of sensor-based performance. This section explores essential sensor types and their specific applications in pipe bundling equipment.
Advanced sensors optimize pipe bundling machine performance by precisely monitoring tension, speed, and material presence. Photoelectric sensors detect material, load cells measure weight, ultrasonic sensors monitor dimensions, and encoders synchronize movement. These sensors enable proactive adjustments, minimize waste, and ensure consistent bundling quality, improving efficiency and reducing downtime.
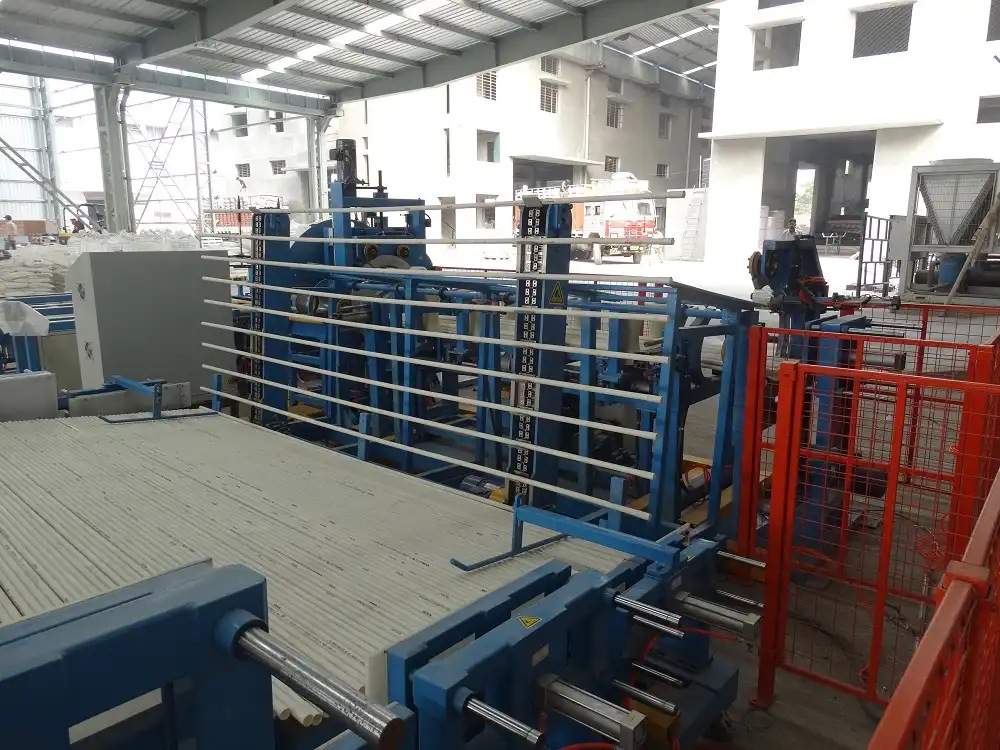
Diving Deeper: Sensor Technology and Targeted Applications
Each sensor type plays a unique role in optimizing pipe bundling. Let’s explore how these sensors can enhance machine performance and overall efficiency.
- Photoelectric Sensors: Guarantee accurate material positioning, preventing misaligned bundles and jams.
- Load Cells: Provide precise weight measurements, guaranteeing accurate filling of each bundle.
- Ultrasonic Sensors: Measure dimensions, ensuring the correct strap size and precise positioning of the sealing mechanism.
- Encoders: Track component position and speed, synchronizing the bundling process.
- Tension Sensors: Monitor strap tension, ensuring secure and consistent bundles.
These targeted applications make it essential to carefully select the appropriate sensors.
Technical Deep Dive: Specific Sensor Features and Benefits
To maximize the impact of advanced sensors, it’s crucial to understand their technical specifications and how they translate into tangible benefits for pipe bundling operations. Here are some key technical details:
- Response Time: Sensors with faster response times provide more immediate feedback, allowing for quicker adjustments and reducing the risk of errors.
- Accuracy: High-accuracy sensors provide more precise measurements, leading to more consistent and reliable bundling.
- Durability: Sensors designed for harsh industrial environments can withstand vibrations, temperature fluctuations, and exposure to dust and debris.
- Communication Protocols: Sensors that support standard communication protocols like IO-Link can be easily integrated into existing control systems.
- Self-Diagnostics: Sensors with self-diagnostic capabilities can detect and report potential issues, allowing for proactive maintenance.
Understanding these technical specifications empowers manufacturers to make informed decisions when selecting sensors for their pipe bundling machines. By choosing sensors that meet their specific requirements, they can optimize performance, minimize downtime, and maximize the overall efficiency of their operations.
Proper sensor selection, installation, and maintenance are important for maximizing its return on investment and optimizing performance.
3. Harnessing Data: Analysis and Proactive Intervention
Sensor data is invaluable if interpreted effectively. This transformation of data into actionable intelligence enables maintenance actions and optimizes pipe bundling operations.
Analyzing sensor data for proactive intervention in pipe bundling involves identifying patterns indicating potential failures. Setting thresholds and generating alerts allows maintenance to schedule interventions, minimizing downtime and maximizing efficiency. Data analysis informs decisions and enhances machine performance.

From Raw Data to Actionable Insights: A Structured Approach
To demonstrate how actionable insights can be derived from sensor data, let’s examine the key steps involved in data analysis and interpretation.
- Data Collection: Continuously collect sensor data for a comprehensive view of machine health.
- Data Pre-processing: Clean and format raw data to ensure accuracy and reliability for analysis.
- Feature Extraction: Identify relevant features such as tension trends, vibration frequencies, or pressure fluctuations.
- Predictive Modeling: Use algorithms to create models predicting future conditions based on current and historical data.
- Alert Generation: Set thresholds that, when exceeded, trigger alerts to the maintenance team.
Table: Sample Data Analysis and Actionable Insights
Data Type | Sensor | Potential Issue | Actionable Insight |
---|---|---|---|
Tension | Load Cell | Fluctuating Tension | Check strap feed mechanism |
Vibration | Accelerometer | Increased Vibration | Inspect motor bearings, check alignment |
Speed | Encoder | Inconsistent Speed | Calibrate sensor, adjust drive system |
This structured approach enables effective data utilization, optimizing machine performance and minimizing potential problems.
By transforming raw sensor data into actionable insights, manufacturers can proactively address potential problems, optimize machine performance, and minimize downtime. This data-driven approach empowers them to make informed decisions and ensure the reliable and efficient operation of their pipe bundling machines.
4. Strategic Implementation of a Sensor-Driven Maintenance Program

Integrating advanced sensors into a maintenance program needs a plan. Successfully transitioning requires addressing technology, integrating data, and personnel training.
Successfully implementing a sensor-driven maintenance strategy involves:
- Assessment: Determine which aspects of operations benefit most from sensor data.
- Deployment: Install sensors strategically.
- Integration: Utilize a platform for data visualization and analysis.
- Training: Teach personnel how to interpret data and address alerts.
Embracing sensor-driven maintenance goes beyond technology; it requires creating a culture of proactive problem-solving and continuous improvement.
Effective integration needs planning, technology deployment, data integration, and continuous refinement. It is a worthwhile investment for improving long-term performance. By embracing Industry 4.0 principles, businesses will become more competitive.
Conclusion
Advanced sensors optimize pipe bundling machine performance. Real-time data and proactive maintenance can reduce downtime, minimize material waste, and improve overall efficiency. Embracing sensor-driven maintenance prepares businesses for success in a competitive market. By embracing smart manufacturing and Industry 4.0 principles, companies can ensure their operations are efficient, sustainable, and profitable.