1. Introduction: Advancing Pallet Wrapping with Rotary Arm Technology
In high-volume logistics and manufacturing, particularly within the food and beverage sectors, efficient and secure pallet wrapping is critical. This article delves into the engineering, specifications, and operational advantages of the Rotary Arm Pallet Packing Machine, often referred to as a vertical stretch wrapper with a rotary arm. This technology offers a robust solution for stabilizing large, heavy, or unstable loads, such as food pallets and water bottle pallets, overcoming the limitations of traditional turntable systems and manual wrapping methods.
2. The Engineering Principle: Why Rotary Arm Wrapping Excels
Traditional turntable wrappers rotate the pallet itself, which can be problematic for tall, lightweight, or unstable loads due to centrifugal forces. The rotary arm stretch wrapper employs a fundamentally different approach:
- Stationary Load: The pallet remains stationary on the floor or conveyor. This eliminates the risk of product shifting or toppling during the wrapping cycle, crucial for delicate or irregularly stacked goods.
- Rotating Film Delivery: A vertical arm, holding the film carriage system, rotates around the stationary pallet. This ensures consistent film application and tension control regardless of load instability.
- High-Speed Capability: Decoupling the load's rotation from the film application allows for potentially higher wrapping speeds compared to turntables handling similarly unstable loads.
This design philosophy directly addresses the challenges faced when wrapping loads prone to instability or requiring high throughput.
3. Core Design, Structure, and Key Components
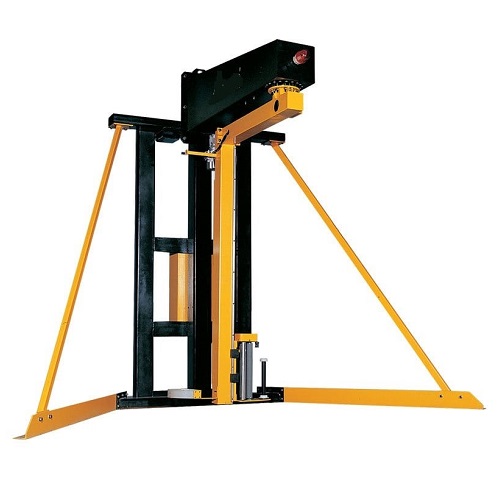
The effectiveness of a rotary arm wrapper stems from its integrated mechanical and control systems. Key components typically include:
- Heavy-Duty Steel Frame: Provides structural rigidity and stability for the rotating arm assembly, ensuring smooth operation even at high speeds. Designed for industrial environments.
- Rotary Arm Assembly: Driven by a robust motor and VFD (Variable Frequency Drive) for controlled acceleration, deceleration, and precise rotational speed (RPM). Often counterbalanced for smooth, vibration-minimized rotation.
- Powered Pre-Stretch Film Carriage: This critical subsystem stretches the film before application (often 150% to 300%+), maximizing film yield, reducing material costs, and ensuring higher load containment force. Tension control systems maintain consistent film force on the load.
- PLC Control System: The machine's brain, typically featuring a Programmable Logic Controller (PLC) and a user-friendly Human-Machine Interface (HMI). Allows operators to select pre-programmed wrap patterns, adjust parameters (top/bottom wraps, arm speed, film tension, pre-stretch ratio), and perform diagnostics.
- Automatic Film Clamp, Cut, and Wipe System: Automates the start and end of the wrapping cycle, improving efficiency and reducing operator intervention. Options range from simple heat seals to more complex wipe-down systems for optimal tail attachment.
- Safety Features: Essential for automated machinery. Commonly includes safety fencing, access gates with interlocks, light curtains at entry/exit points, emergency stop buttons, and arm rotation obstruction sensors, complying with relevant safety standards (e.g., ISO 13849-1).
4. Technical Specifications and Performance Data Comparison
Understanding the machine's capabilities requires examining its technical data. Here are typical specifications for a robust rotary arm pallet wrapper, contrasted where relevant:
- Maximum Load Size (L x W x H): Typically up to 1300mm x 1300mm x 2400mm (or higher, customizable). Handles larger/taller loads than many standard turntables.
- Maximum Load Weight: Often unlimited, as the load sits directly on the floor or heavy-duty conveyor. Significant advantage over turntables with weight limits (e.g., 2000 kg).
- Rotary Arm Speed: Variable, up to 15-30 RPM (or higher on performance models).
- Wrapping Efficiency (Throughput): 30-60+ pallets per hour, depending on load height, wrap pattern, and integration. Comparable or potentially higher than turntables for unstable loads.
- Film Pre-Stretch Ratio: Standard 250%, adjustable electronically via HMI (e.g., 150% - 300%+). Maximizes film efficiency.
- Film Type: Standard LLDPE stretch film, 500mm width, up to 76mm core diameter.
- Power Requirements: Typically 400V/3Ph/50Hz (or customized), ~2.5 kW.
- Control System: Siemens or Allen-Bradley PLC with color touch-screen HMI.
- Machine Footprint: Requires adequate clearance for arm rotation; specific dimensions vary by model and safety guarding.
rotary arm pallet
Data Comparison Point: - Rotary Arm: Ideal for unstable/tall/heavy loads, stationary placement prevents shifting. Throughput less affected by load instability.
- Turntable: Better suited for stable, moderate-weight loads. Potential for higher throughput on stable loads due to simpler mechanics. More compact footprint generally.
5. Operational Workflow and User Experience
Operating a modern rotary arm wrapper is designed for efficiency and ease of use:
- Pallet Placement: The pallet load is placed in the designated wrapping zone, typically via forklift, pallet jack, or integrated conveyor system.
- Cycle Initiation: The operator selects the desired wrap program on the HMI or uses a remote control/pull cord.
- Automatic Wrapping:
- The film is automatically clamped to the pallet base (or load).
- The rotary arm begins rotating, applying film according to the programmed top/bottom wraps and overlap settings.
- The film carriage moves vertically on its mast to cover the entire height of the load.
- Pre-stretch and tension are continuously controlled.
- Film Cut & Secure: Upon cycle completion, the film is automatically cut and wiped/sealed against the load.
- Pallet Removal: The wrapped pallet is ready for removal.
User Experience:
- Intuitive HMI: Modern touch screens allow easy parameter adjustments, program storage (for different load types), and access to diagnostics and maintenance alerts.
- Reduced Manual Labor: Eliminates physically demanding and inconsistent hand wrapping.
- Maintenance: Routine checks involve inspecting film carriage rollers, drive belts/chains, safety sensors, and periodic lubrication as guided by the HMI or manual. Film roll changes are typically straightforward.
6. Quantifiable Benefits of Rotary Arm Wrapping Technology
Investing in a rotary arm stretch wrapper delivers tangible advantages:
- Enhanced Load Stability & Product Protection: Consistent tension and pre-stretch create a secure, tight wrap, minimizing damage during transit, especially critical for food and beverage products. Stationary wrapping prevents in-cycle load shifting.
- Increased Throughput: Automation significantly speeds up the packaging process compared to manual or semi-automatic methods, directly impacting overall line efficiency (e.g., achieving 45 pallets/hour vs. 10-15 manually).
- Reduced Film Consumption: Powered pre-stretch can reduce film usage by 50-75% compared to hand wrapping or machines without pre-stretch, leading to significant cost savings and environmental benefits. A 250% pre-stretch turns 1 meter of film into 3.5 meters on the pallet.
- Lower Labor Costs: Frees up personnel previously dedicated to wrapping for other value-added tasks. Reduces risk of repetitive strain injuries.
- Improved Safety: Integrated safety systems create a controlled, guarded environment, significantly safer than manual wrapping around moving forklifts or turntables.
- Versatility: Capable of handling a wide range of pallet sizes, weights, and configurations with simple program adjustments.
7. Application Spotlight: Optimizing Food & Beverage Palletizing
The food and beverage industry particularly benefits from rotary arm wrappers:
- Handling Unstable Loads: Effectively wraps pallets of PET bottles, cans, glass containers, or bagged goods that might shift on a turntable.
- Maintaining Product Integrity: Gentle, consistent wrapping protects packaging and prevents product damage.
- Hygiene Considerations: Stainless steel options or specific component shielding can be available for environments requiring washdown capabilities.
- High Volume: Meets the demands of fast-paced production lines common in this sector.
8. Integration and Customization Pathways
Rotary arm wrappers can be standalone units or integrated into fully automated packaging lines:
- Conveyor Integration: Seamless connection with infeed and outfeed pallet conveyors for fully automated flow.
- Automatic Top Sheet Dispenser: Applies a protective top sheet for dust or moisture protection before wrapping begins.
- Roping Devices: Creates a reinforced "rope" at the top and/or bottom of the pallet for extra stability.
- Custom Guarding & Footprint: Designs can be adapted to specific plant layouts and safety requirements.
- Environmental Packages: Options for operation in cold storage or demanding industrial conditions.
9. Conclusion: A Strategic Investment in Packaging Efficiency
The Vertical Stretch Wrapper with Rotary Arm represents a significant advancement in palletizing technology. By addressing the core challenges of wrapping large, heavy, or unstable loads, it delivers improvements in load security, throughput, material efficiency, labor utilization, and operational safety. For businesses, especially in the food, beverage, and high-volume distribution sectors, adopting this technology is a strategic investment towards optimizing the end-of-line packaging process and ensuring products reach their destination intact.
10. Frequently Asked Questions (FAQs)
-
How does the rotary arm improve efficiency for large food pallets?
By keeping the heavy/unstable food pallet stationary, the rotary arm can wrap quickly and consistently without risking product shift or collapse, unlike turntable systems. This allows for higher, more reliable throughput. -
What is the typical pre-stretch percentage and how does it save film?
Typical pre-stretch is 250%, meaning 1 meter of film is stretched to 3.5 meters as it's applied. This drastically reduces the amount (and cost) of film consumed per pallet compared to systems with lower or no pre-stretch. Higher percentages (up to 300%+) are possible. -
How does the rotary arm handle unstable loads compared to a turntable wrapper?
The key difference is the stationary load. Turntables rotate the load itself, and centrifugal force can cause tall or poorly stacked items to shift or fall. Rotary arms spin around the stationary load, eliminating this force and providing a much more stable wrapping process. -
What safety standards do these machines typically meet?
Reputable machines are designed to meet international and regional safety standards, such as CE (Europe), UL (North America), and ISO 13849-1 (Safety of machinery - Safety-related parts of control systems). Key features include interlocked guarding, light curtains, and emergency stops. -
What are the typical maintenance requirements?
Routine maintenance includes daily checks of safety features, periodic cleaning, inspection of film carriage rollers and belts/chains, and lubrication according to the manufacturer's schedule (often prompted by the HMI). Film roll changes are a regular operational task. -
Can this machine be integrated into an existing automated line?
Yes, rotary arm wrappers are commonly designed for integration. They can interface with upstream and downstream conveyors, palletizers, and plant control systems (using protocols like Ethernet/IP, Profinet) for seamless automation.
Contact Us Now
Ready to transform your packaging process for challenging loads like food and water bottom pallets? Contact us today for a detailed consultation, custom quote, or to explore how a rotary arm stretch wrapper can meet your specific operational needs and deliver measurable ROI. Let's enhance your packaging efficiency and reliability.