Automatic coiler for corrugated hose & plastic pipe
In modern manufacturing, particularly within the extrusion sector for piping and hosing, automation is key to achieving efficiency, consistency, and cost-effectiveness. This automatic coiling machine represents a significant advancement in the downstream handling of corrugated hoses and various plastic pipes (such as PE, PVC, PEX). Designed for seamless integration into production lines, it automates the coiling, winding, and strapping processes, minimizing manual intervention and boosting overall throughput. This article provides a technical overview of its design, components, operational parameters, and user benefits, reflecting the precision and engineering focus valued in the industry, akin to standards seen in publications like MM MaschinenMarkt.
1. Core Functionality and Operating Principle
The machine operates through a synchronized sequence of actions controlled by a central processing unit. The core process involves:
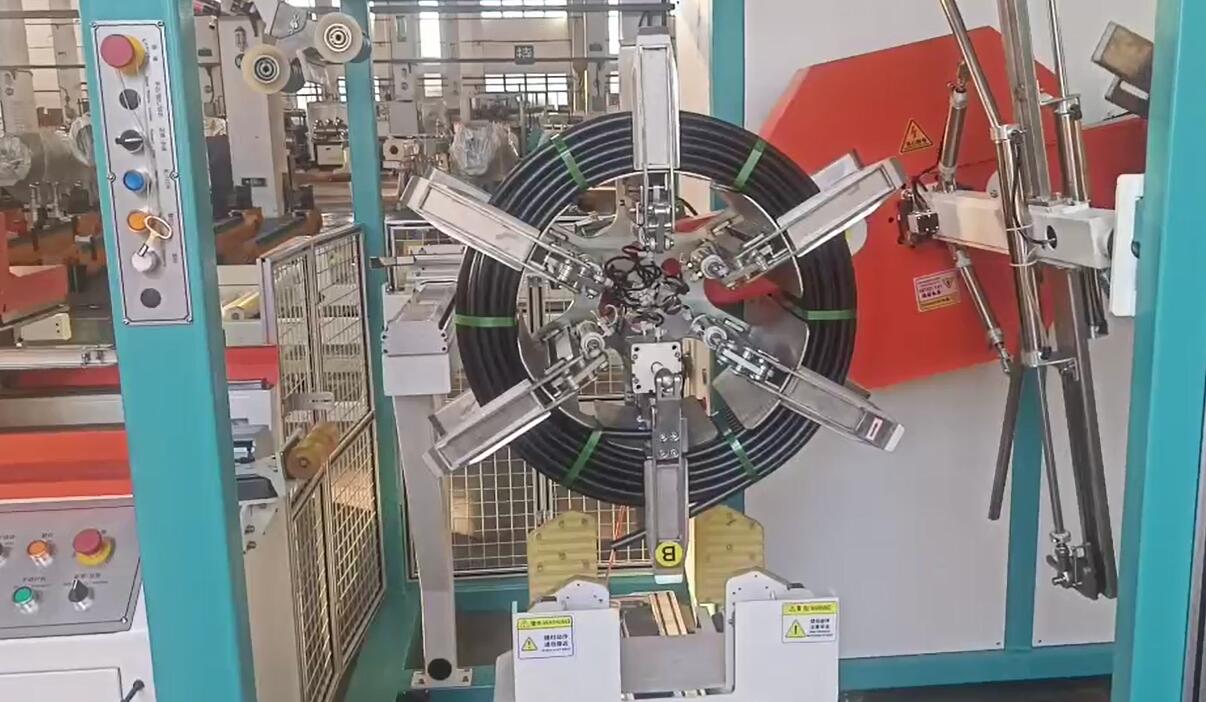
- Pipe/Hose Infeed: The pipe or hose enters the machine, often directly from an extruder or haul-off unit. An optional automatic dispenser or accumulator can manage slack and ensure consistent tension.
- Precision Winding: The pipe is guided onto a rotating coiling head (mandrel). A traversing unit moves back and forth across the width of the coiling head, ensuring the pipe is layered evenly and precisely, creating a stable and compact coil. Winding speed is typically synchronized with the extrusion line speed.
- Length Measurement & Cutting: Integrated sensors or encoders measure the pipe length accurately. Once the preset length is reached, the line momentarily pauses (or speed is adjusted via an accumulator), and an automatic cutter cleanly severs the pipe.
- Automatic Strapping: The completed coil is then secured using Polypropylene (PP) straps. An automatic strapping unit applies, tensions, seals, and cuts the straps at pre-programmed positions (typically 2 to 4 straps per coil).
- Coil Ejection: Once strapped, the coiling head segments may retract, allowing the finished coil to be automatically ejected onto a conveyor, tilting table, or designated collection area.
2. Key Components and Design Features
The robust performance and reliability of this automatic coiler stem from its carefully engineered components:
- Machine Frame: Constructed from heavy-gauge steel, providing rigidity and vibration damping, essential for high-speed operation and consistent coil quality. Powder-coated or treated for corrosion resistance in industrial environments.
- Coiling Head/Mandrel: Typically features adjustable core diameter segments to accommodate different coil inner diameters (IDs). Designed for quick collapse or segment retraction for easy coil removal. Surface treatment ensures smooth contact with the pipe material.
- Traversing Unit: Servo-driven or precisely geared motor system ensures accurate and repeatable layering of the pipe. Programmable pitch control allows for adjustments based on pipe diameter and desired coil density.
- Cutting Unit: Utilizes high-strength blades (e.g., shear type or rotary) designed for clean, burr-free cuts on various plastic materials. Actuation is typically pneumatic or servo-electric for speed and precision.
- Automatic Strapping Head: A critical component, often sourced from specialized manufacturers. Features adjustable tension control, reliable strap feeding, and heat-sealing or friction-weld sealing mechanisms for PP straps.
- Control System: The brain of the machine. Usually incorporates a Programmable Logic Controller (PLC) (e.g., Siemens, Allen-Bradley, Omron) for managing all sequences, speeds, and interlocks. A Human-Machine Interface (HMI), often a touchscreen panel, provides operator control, parameter setting (coil length, strap number/position, diameters), diagnostics, and production data display.
3. Technical Specifications Overview
While specific parameters vary by model and customization, typical specifications include:
- Applicable Pipe/Hose OD Range: 10 mm – 75 mm (model dependent)
- Maximum Coil Outer Diameter (OD): Up to 1500 mm
- Adjustable Coil Inner Diameter (ID): 200 mm – 800 mm (typical range)
- Adjustable Coil Width: 100 mm – 600 mm
- Maximum Coiling Speed: Up to 100 m/min (synchronized with line speed)
- Length Measurement Accuracy: ± 0.1% - 0.5% (depending on system)
- Strapping Material: Polypropylene (PP) strap
- Strap Width: 9 mm – 16 mm (typical)
- Number of Straps per Coil: 2 - 4 (programmable positions)
- Control System: PLC + Touchscreen HMI
- Drive System: Servo motors / AC motors with VFDs
- Power Supply: 380V/415V, 50/60Hz, 3-Phase (or as per requirement)
- Air Supply: 6-8 bar (for pneumatic components)
4. Integration into Automated Production Lines
This automatic coiler is rarely a standalone unit. Its true value is realized when integrated into a complete extrusion and packaging line. Key integration aspects include:
- Synchronization: Directly interfaces with the extruder and haul-off unit via speed signals (e.g., 0-10V analog or digital communication like Profinet/EtherNet/IP) to precisely match the production speed.
- Communication: Can communicate upstream and downstream with other equipment (e.g., receiving signals from extruder, sending signals to subsequent packaging or palletizing systems).
- Modularity: Designed as part of a larger automated system, potentially including buffer accumulators, quality control stations (diameter/ovality checks), and downstream packaging solutions.
5. Available Options and Customization
To meet diverse production needs, several options can enhance the coiler's capabilities:
- Automatic Labeling System: Applies pre-printed or print-and-apply labels with product information, barcodes, or QR codes directly onto the coil or strap.
- Automatic Coil Ejection & Stacking: Robotic arms or conveyor systems can transfer finished coils to pallets or designated stacking areas, creating fully automated palletizing solutions.
- Advanced Coil Packaging: Integration with stretch wrappers or shrink tunnels for further protection and unitization of coils.
- Automatic Coil Weighing: Integrated load cells for capturing and recording the weight of each coil.
- Data Logging and Connectivity: Enhanced PLC/HMI features for production data logging (coils produced, lengths, downtimes), remote monitoring, and integration with Manufacturing Execution Systems (MES) or SCADA systems for Industry 4.0 initiatives (often referred to as level one/two system integration).
- Custom Mandrel Designs: Specific mandrel sizes or surface finishes for delicate or unique pipe profiles.
6. User Experience and Operational Benefits
From an operational standpoint, incorporating this automatic coiler offers tangible advantages:
- Reduced Labor Costs: Significantly minimizes the manual labor required for coiling, strapping, and handling, freeing up personnel for higher-value tasks.
- Improved Consistency: Automated processes ensure every coil meets consistent length, dimension, and strapping specifications, enhancing product quality and customer satisfaction.
- Increased Throughput: Capable of operating at high speeds matching modern extrusion lines, eliminating downstream bottlenecks.
- Enhanced Safety: Enclosed design with safety interlocks on access doors reduces operator exposure to moving parts, improving workplace safety compared to manual or semi-automatic methods.
- User-Friendly Operation: Modern HMI interfaces provide intuitive controls for setup, parameter adjustments, recipe management, and troubleshooting diagnostics.
- Material Savings: Precise length measurement minimizes pipe scrap compared to manual cutting. Optimized strapping reduces consumable usage.
Conclusion
The automatic coiling machine for corrugated hoses and plastic pipes is an indispensable asset for manufacturers seeking to optimize their extrusion downstream processes. Its robust design, precise control systems, and integration capabilities deliver significant improvements in efficiency, consistency, safety, and cost-effectiveness. By automating the labor-intensive tasks of coiling and strapping, it allows producers to maintain competitiveness in demanding markets.
For detailed specifications tailored to your application or to discuss integration possibilities, please visit the manufacturer's page or contact their technical team.
https://www.fhopepack.com/Automatic-Coiling-Machine/
info@fhopepack.com